Are American Workers Ready For The Return Of Manufacturing Jobs?
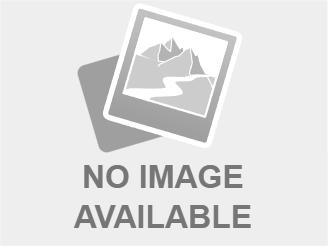
Table of Contents
The Skills Gap in the Modern Manufacturing Sector
The modern manufacturing sector is vastly different from its predecessors. The rise of automation and advanced technologies has created a significant skills gap, presenting a challenge to the resurgence of manufacturing jobs.
Automation and the Need for Specialized Skills
Modern factories are increasingly reliant on automation, robotics, and sophisticated software systems. This shift necessitates a workforce with specialized skills to operate, maintain, and program these advanced technologies. The demand for skilled technicians and engineers far outweighs the current supply.
- Increased demand for automation specialists: Robotics technicians, PLC (Programmable Logic Controller) programmers, and automation engineers are in high demand. These roles require specialized training and expertise in complex systems.
- Shortage of skilled maintenance personnel: Sophisticated equipment requires highly skilled maintenance personnel capable of troubleshooting and repairing intricate machinery. A lack of these skilled workers can lead to costly downtime and production delays.
- Need for data analysts: Modern manufacturing relies heavily on data analysis to optimize production processes and improve efficiency. Data analysts are crucial for interpreting large datasets and identifying areas for improvement.
The Decline of Traditional Manufacturing Skills
The outsourcing of manufacturing jobs in previous decades led to a decline in traditional manufacturing skills. While some of these skills remain relevant, many require updating to adapt to modern technologies. This necessitates comprehensive retraining and upskilling programs.
- Lack of experienced machinists, welders, and other skilled tradespeople: The shortage of experienced workers in these crucial trades hinders the ability of companies to scale up production.
- Need for bridging programs: Bridging programs are essential to help workers with existing skills transition to new technologies and roles within the modernized manufacturing sector.
- Importance of apprenticeships and vocational training: Investing in robust apprenticeship and vocational training programs is vital to cultivate the next generation of skilled manufacturing workers.
Government and Private Sector Initiatives to Bridge the Skills Gap
Addressing the skills gap requires a collaborative effort between the government and the private sector. Numerous initiatives are underway to provide training and education opportunities for American workers.
Government-Funded Training Programs
Federal and state governments are investing in various workforce development programs aimed at boosting the manufacturing workforce. These programs offer grants, apprenticeships, and training opportunities focused on the skills needed in modern manufacturing.
- Examples of successful grant programs: The Department of Labor and other agencies provide funding for training programs focused on specific manufacturing technologies and skills.
- Analysis of the effectiveness of apprenticeship programs: Apprenticeships provide a valuable pathway for young people to gain hands-on experience and develop crucial skills. Evaluating their effectiveness is crucial to refining these programs.
- Discussion of community college initiatives: Community colleges play a vital role in providing affordable and accessible training programs, offering reskilling and upskilling opportunities for workers.
Private Sector Investments in Workforce Development
Companies are increasingly recognizing the importance of investing in their own workforce. Many leading manufacturers are launching internal training programs and apprenticeships to develop and retain skilled employees.
- Examples of companies offering on-the-job training and apprenticeships: Many successful manufacturers are implementing robust training programs to upskill existing employees and attract new talent.
- Discussion of the benefits of company-sponsored education programs: Companies that invest in employee education often see increased productivity, improved employee retention, and a more skilled workforce.
- Analysis of the impact of these initiatives on employee retention and productivity: Data demonstrating the return on investment from these initiatives is essential for encouraging further investment in workforce development.
The Evolving Nature of Manufacturing Jobs and the American Worker's Adaptability
The perception of manufacturing jobs has changed significantly. Modern manufacturing facilities often offer higher wages, improved working conditions, and opportunities for career advancement.
Higher Wages and Improved Working Conditions
Contrary to outdated stereotypes, many modern manufacturing jobs offer competitive salaries and benefits packages, making them attractive to a wider range of workers.
- Comparison of wages in manufacturing vs. other sectors: In many regions, manufacturing jobs now offer wages comparable to or exceeding those in other sectors.
- Improved safety standards and working conditions: Modern factories prioritize safety and incorporate advanced technologies to improve working conditions significantly.
- Increased benefits packages: Many manufacturing companies offer comprehensive benefits packages, including health insurance, retirement plans, and paid time off, making them more attractive employers.
The Importance of Adaptability and Lifelong Learning
The rapid pace of technological advancement in manufacturing means that continuous learning and adaptability are crucial for success. Workers need to embrace lifelong learning to remain competitive and adapt to evolving technologies.
- Importance of continuous skills development and retraining: Workers need access to resources and opportunities for continuous training to keep their skills up-to-date.
- The role of online learning platforms and resources: Online learning platforms offer flexible and accessible training options, making it easier for workers to upskill and reskill.
- The value of embracing new technologies and processes: A willingness to learn and adapt to new technologies and processes is crucial for success in the modern manufacturing environment.
Conclusion
The resurgence of manufacturing jobs in the US presents both opportunities and challenges. While a skills gap exists, government and private sector initiatives are working to address it. The evolving nature of manufacturing work and the potential for higher wages and improved working conditions make the sector attractive, but adaptability and lifelong learning will be crucial for American workers to thrive in this new landscape of manufacturing jobs. To ensure the success of the resurgent manufacturing sector, continued investment in worker training and education is vital. By addressing the skills gap and fostering a culture of lifelong learning, America can seize the opportunity presented by the return of manufacturing jobs and build a robust and competitive manufacturing workforce for the future.
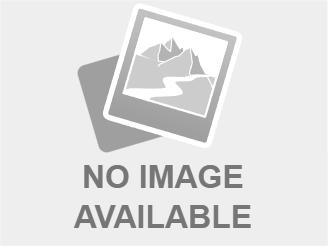
Featured Posts
-
Family Tragedy Two Dead Children Injured After Train Collision
May 20, 2025 -
Ferrari Lekler I Khemilton Spornaya Diskvalifikatsiya Posle Gonki
May 20, 2025 -
Katalogos Efimereyonton Giatron Patras 12 And 13 Aprilioy
May 20, 2025 -
Jennifer Lawrences Second Child A New Addition To The Family
May 20, 2025 -
L Affaire Jaminet Conclue Remboursement De 450 000 Euros Au Stade Toulousain
May 20, 2025