Automated Visual Inspection Of Lyophilized Vials: Challenges And Solutions
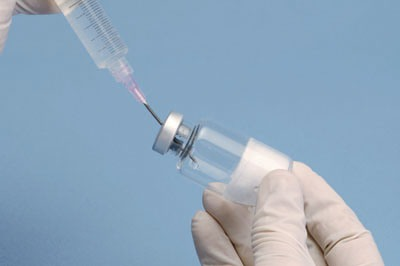
Table of Contents
Challenges in Automated Visual Inspection of Lyophilized Vials
Implementing automated visual inspection for lyophilized vials is not without its hurdles. Several factors contribute to the complexity of achieving reliable and consistent results.
Variability in Lyophilized Product Appearance
Lyophilized products exhibit considerable variations in appearance due to the inherent complexities of the freeze-drying process. These variations can significantly impact the accuracy of automated inspection systems. Consistent detection of defects becomes challenging due to the subtle differences between acceptable variations and actual defects.
- Variations in cake height and structure: The height and structure of the lyophilized cake can vary, making consistent image analysis difficult.
- Presence of cracks, fissures, or delamination: Cracks, fissures, and delamination are common defects that require precise detection.
- Discoloration or other visual defects: Subtle color changes or other visual defects can indicate quality issues and need to be identified reliably.
- Presence of particulate matter: Foreign particulate matter within the vial is a critical quality concern requiring sensitive detection.
- Difficulties in differentiating between acceptable variations and defects: Distinguishing between natural variations in the lyophilization process and actual defects poses a significant challenge for automated systems. This requires sophisticated algorithms capable of learning and adapting to various product appearances.
Lighting and Imaging Challenges
Achieving optimal lighting conditions for capturing subtle defects is crucial for successful automated visual inspection. Lyophilized vials present unique lighting challenges due to their reflective surfaces and the need to highlight minute defects.
- Minimizing reflections from the vial surface: Reflections from the glass vial surface can obscure defects, requiring careful lighting control and image processing techniques.
- Ensuring uniform illumination across the vial: Consistent illumination is essential to prevent shadows and uneven lighting that can mask defects.
- Optimizing image contrast to highlight defects: Enhancement of image contrast is necessary to make subtle defects more visible to the automated system.
- Dealing with variations in vial material and color: Different vial materials and colors can affect light transmission and reflection, demanding adaptable lighting and image processing strategies.
- Selecting appropriate imaging techniques (e.g., brightfield, darkfield): The choice of imaging technique significantly impacts the visibility of different types of defects.
High-Throughput Requirements
Pharmaceutical manufacturing demands high-speed inspection systems to keep pace with production needs. Balancing speed with accuracy and sensitivity presents a significant challenge in automated visual inspection of lyophilized vials.
- Need for high-speed imaging and processing: High-speed cameras and efficient image processing algorithms are crucial for maintaining throughput.
- Minimizing inspection time per vial: Reducing inspection time per vial is critical for maximizing productivity without compromising accuracy.
- Maintaining accuracy at high throughput: High throughput should not come at the expense of accuracy; the system must maintain a high level of defect detection even at high speeds.
- Integrating with existing production lines: Seamless integration with existing manufacturing equipment and processes is vital for efficient implementation.
- Balancing speed and sensitivity: Optimizing the system to achieve the right balance between speed and sensitivity is a key design consideration.
Solutions for Efficient Automated Visual Inspection
Overcoming the challenges of automated visual inspection of lyophilized vials necessitates the implementation of advanced technologies and innovative approaches.
Advanced Imaging Techniques
Employing advanced imaging techniques enhances the sensitivity and accuracy of defect detection. These methods provide more detailed information about the vial's contents and surface characteristics.
- Multispectral imaging for enhanced contrast: Multispectral imaging utilizes multiple wavelengths of light to improve contrast and highlight defects that might be invisible under standard lighting.
- Hyperspectral imaging for detailed material analysis: Hyperspectral imaging captures a wide range of wavelengths, providing detailed spectral information about the lyophilized product and enabling more precise defect identification.
- 3D imaging for better visualization of surface defects: 3D imaging techniques create a three-dimensional representation of the vial's contents, facilitating better visualization and detection of surface defects.
- AI-powered image analysis for improved defect recognition: Artificial intelligence plays a critical role in analyzing complex images, learning from examples, and adapting to variations in product appearance.
Intelligent Image Analysis Algorithms
Sophisticated algorithms, particularly those utilizing machine learning and artificial intelligence (AI), are crucial for handling the variability inherent in lyophilized products.
- Machine learning for defect classification: Machine learning algorithms can be trained to recognize and classify various defects based on large datasets of images.
- AI-powered image segmentation: AI-powered image segmentation techniques isolate individual defects from the background, enhancing accuracy and reducing false positives.
- Deep learning for improved accuracy: Deep learning models, a subset of machine learning, can learn complex patterns and improve the accuracy of defect detection.
- Adaptive algorithms for handling variability: Adaptive algorithms adjust to variations in product appearance, ensuring consistent performance despite the inherent variability of lyophilized products.
System Integration and Data Management
Seamless integration with existing manufacturing systems and robust data management are crucial for efficient operation and regulatory compliance.
- Automated data logging and reporting: Automated systems should log inspection results and generate comprehensive reports for quality control and regulatory compliance.
- Integration with MES (Manufacturing Execution System): Integration with MES systems provides real-time data visibility and facilitates efficient process control.
- Real-time monitoring and analysis: Real-time monitoring and analysis capabilities enable immediate identification and resolution of potential issues.
- Compliance with industry regulations (e.g., 21 CFR Part 11): Automated visual inspection systems must comply with relevant industry regulations to ensure data integrity and traceability.
Conclusion
Automated visual inspection of lyophilized vials offers significant advantages in terms of speed, accuracy, and consistency compared to manual methods. However, addressing the challenges related to product variability, lighting, and throughput requires implementing advanced imaging techniques, intelligent algorithms, and robust data management. By embracing these solutions, pharmaceutical manufacturers can ensure the quality and integrity of their lyophilized products while optimizing efficiency. Investing in advanced solutions for automated visual inspection of lyophilized vials is crucial for maintaining high production standards and fulfilling regulatory requirements. Consider exploring the advanced options available for automated visual inspection of lyophilized vials to enhance your quality control and overall efficiency.
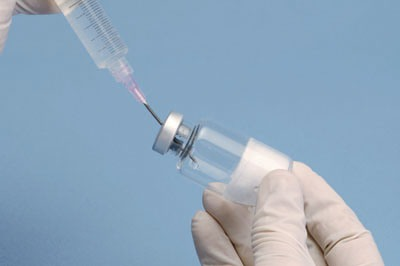
Featured Posts
-
Confirmed Crazy Rich Asians Series Coming To Max
May 12, 2025 -
Match Bayern Inter Le Role Decisif De Mueller
May 12, 2025 -
Selena Gomez And Benny Blanco No First Dance At Wedding
May 12, 2025 -
Thomas Mueller Till Mls Senaste Nytt Och Rykten
May 12, 2025 -
Rochelle Humes Chic New Hairstyle At London Fashion Week
May 12, 2025
Latest Posts
-
I Fonitiki Roytina Tis Tzesika Simpson Ena Amfilegomeno Mystiko
May 12, 2025 -
Tzesika Simpson I Alitheia Piso Apo Tis Fimes Gia Ti Foni Tis
May 12, 2025 -
Luxury Living Notable Homes Showcased On Mtv Cribs
May 12, 2025 -
I Foni Tis Tzesika Simpson Mythos I Pragmatikotita I Methodos Me To Fidisio Sperma
May 12, 2025 -
New Music From Jessica Simpson Thanks To Eric Johnsons Support
May 12, 2025