Automated Visual Inspection Of Lyophilized Vials: Current Limitations And Future Directions
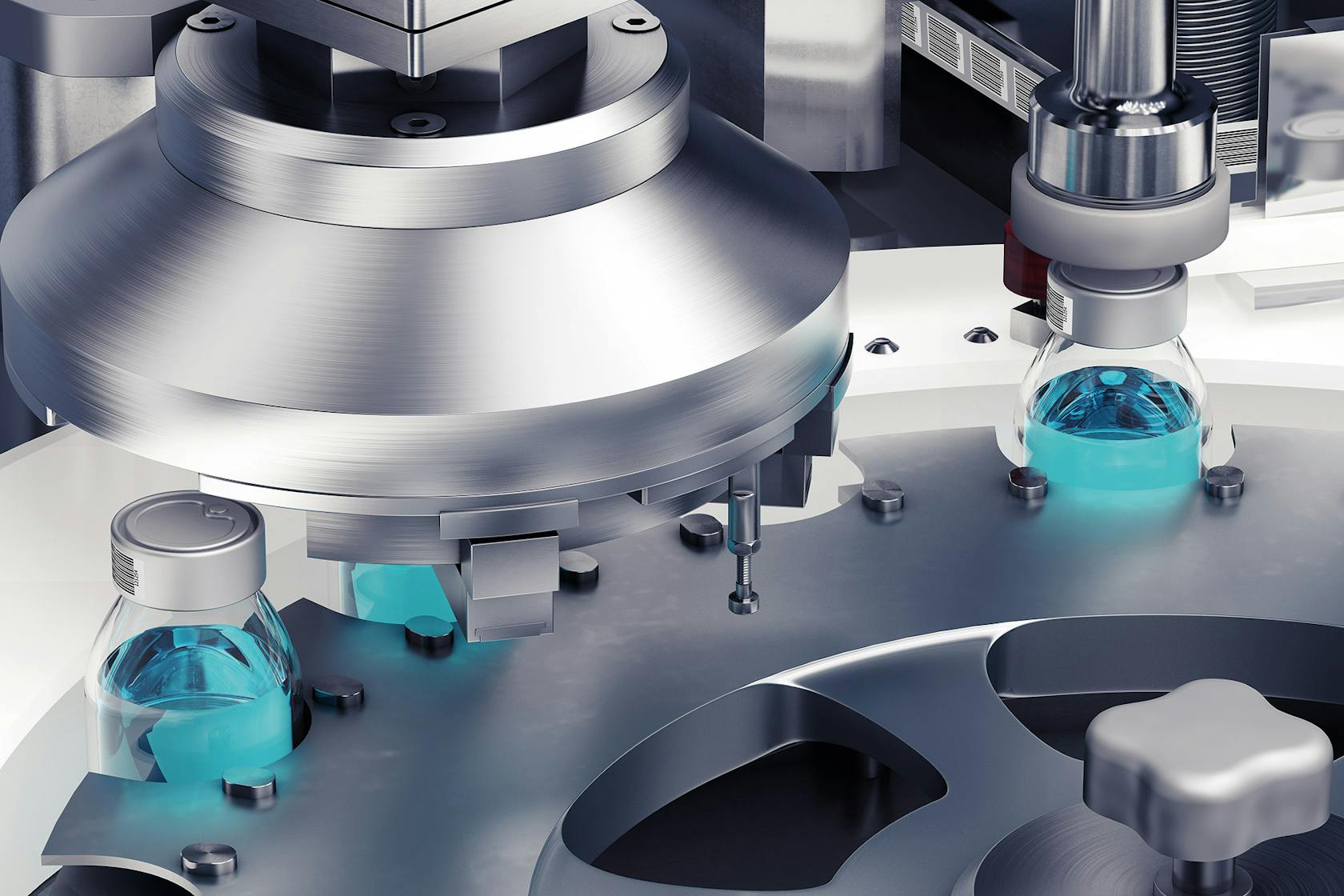
Table of Contents
Current Limitations of Automated Visual Inspection in Lyophilized Vials
Despite the advantages, implementing effective AVI for lyophilized vials presents significant challenges. These limitations stem from complexities in image acquisition, limitations in current defect detection algorithms, and substantial cost and implementation hurdles.
Challenges in Image Acquisition
Acquiring high-quality images of lyophilized vials poses considerable difficulties. The inherent characteristics of these vials, including their transparency and the often-subtle variations in the lyophilized cake, create significant obstacles for automated systems.
- Uneven lighting: Variations in lighting can lead to shadowing, obscuring potential defects and hindering accurate analysis.
- Penetration difficulties: The glass vial itself can impede light penetration, making it challenging to obtain clear images of the lyophilized cake.
- Lyophilized cake variability: Variations in the cake's color, texture, and structure can be misinterpreted as defects by the system.
- High background noise: Noise from various sources can interfere with image clarity, complicating the defect detection process.
These image acquisition challenges necessitate robust solutions focusing on optimized lighting systems and advanced image processing techniques to improve contrast and minimize noise. Effective image acquisition is the cornerstone of successful defect detection in lyophilized vials.
Limitations in Defect Detection Algorithms
Developing algorithms capable of accurately identifying a broad range of defects in lyophilized vials is a complex undertaking. The algorithms must be sophisticated enough to differentiate between acceptable variations and actual critical defects. Current limitations include:
- False positives/negatives: Existing algorithms sometimes incorrectly identify acceptable variations as defects (false positives) or miss actual defects (false negatives).
- Subtle defect detection: Detecting subtle defects such as cracks, particulate matter, or discoloration remains a challenge.
- Algorithm training data limitations: The performance of these algorithms heavily relies on the quality and quantity of training data. Insufficient or biased data can lead to inaccurate results.
- Lack of standardization: A lack of standardization in defect classification across the industry complicates algorithm development and validation.
Addressing these limitations requires advancements in artificial intelligence (AI) and machine learning (ML), leading to more robust and reliable defect detection algorithms. The incorporation of image processing techniques for enhanced feature extraction is also crucial.
Cost and Implementation Challenges
The implementation of AVI systems for lyophilized vials involves significant costs and challenges. The high initial investment is a major deterrent for many pharmaceutical companies.
- High capital expenditure: Purchasing and installing AVI systems represents a significant financial commitment.
- System integration: Integrating AVI systems into existing production lines can be complex and time-consuming.
- Specialized training: Operating and maintaining AVI systems requires specialized training and expertise.
- Ongoing costs: Ongoing maintenance, validation, and software updates also add to the overall cost.
Therefore, achieving cost-effectiveness and a reasonable return on investment (ROI) are essential for the widespread adoption of AVI in the pharmaceutical industry. Improved system design and more efficient system integration strategies are vital to overcome these obstacles.
Future Directions for Automated Visual Inspection of Lyophilized Vials
Despite the current limitations, the future of AVI for lyophilized vials is bright, fueled by advancements in imaging technologies, AI-driven defect classification, and increased standardization efforts.
Advanced Imaging Technologies
Emerging imaging techniques hold immense potential for enhancing the accuracy and reliability of automated visual inspection.
- Hyperspectral imaging: This technique captures detailed spectral information, providing enhanced contrast and significantly improving the ability to identify subtle defects.
- 3D imaging: 3D imaging allows for a comprehensive view of the lyophilized cake, improving the accuracy of defect characterization and reducing false positives.
These advanced imaging techniques offer improved contrast and resolution, ultimately leading to more reliable defect detection capabilities. The ability to reconstruct a 3D model of the vial allows for better defect characterization and improved quality control.
AI-Driven Defect Classification
The application of AI and ML offers a powerful approach to improving the accuracy and efficiency of defect classification.
- Improved algorithm accuracy: AI-powered algorithms can learn from vast datasets, adapting to different vial characteristics and defect types.
- Reduced false positives/negatives: Self-learning algorithms can continuously improve their accuracy over time.
- Self-learning algorithms: These algorithms adapt to variations in lighting, cake appearance, and other factors.
- Improved defect characterization: AI can provide more detailed information about the nature and severity of detected defects.
The use of deep learning techniques and self-learning algorithms will be pivotal in realizing the full potential of AI and machine learning in automated visual inspection.
Standardization and Regulatory Compliance
Standardization is crucial for facilitating broader adoption of AVI. Harmonized standards will streamline validation processes and reduce ambiguity.
- Industry standards: The development of industry-wide standards for defect classification is essential for interoperability and comparability.
- Regulatory guidelines: Clear regulatory guidelines from agencies like the FDA are necessary to ensure the acceptance and validation of AVI systems.
- Validation protocols: Standardized validation protocols are needed to establish the reliability and accuracy of AVI systems.
- International harmonization: Harmonizing international standards will promote consistency and simplify global adoption.
Improved regulatory compliance through clear standards and protocols will be crucial for accelerating the deployment of AVI systems and realizing its transformative potential.
The Future of Automated Visual Inspection for Lyophilized Vials
In conclusion, while current automated visual inspection of lyophilized vials faces challenges related to image acquisition, algorithm limitations, and implementation costs, the future holds tremendous promise. Advancements in advanced imaging technologies, AI-driven defect classification, and standardization efforts are paving the way for more accurate, efficient, and cost-effective solutions. We encourage further research and development in this critical area, emphasizing the need for collaboration between industry, researchers, and regulatory bodies to overcome remaining hurdles and realize the full potential of automated visual inspection of lyophilized vials for enhanced quality control and improved pharmaceutical manufacturing efficiency.
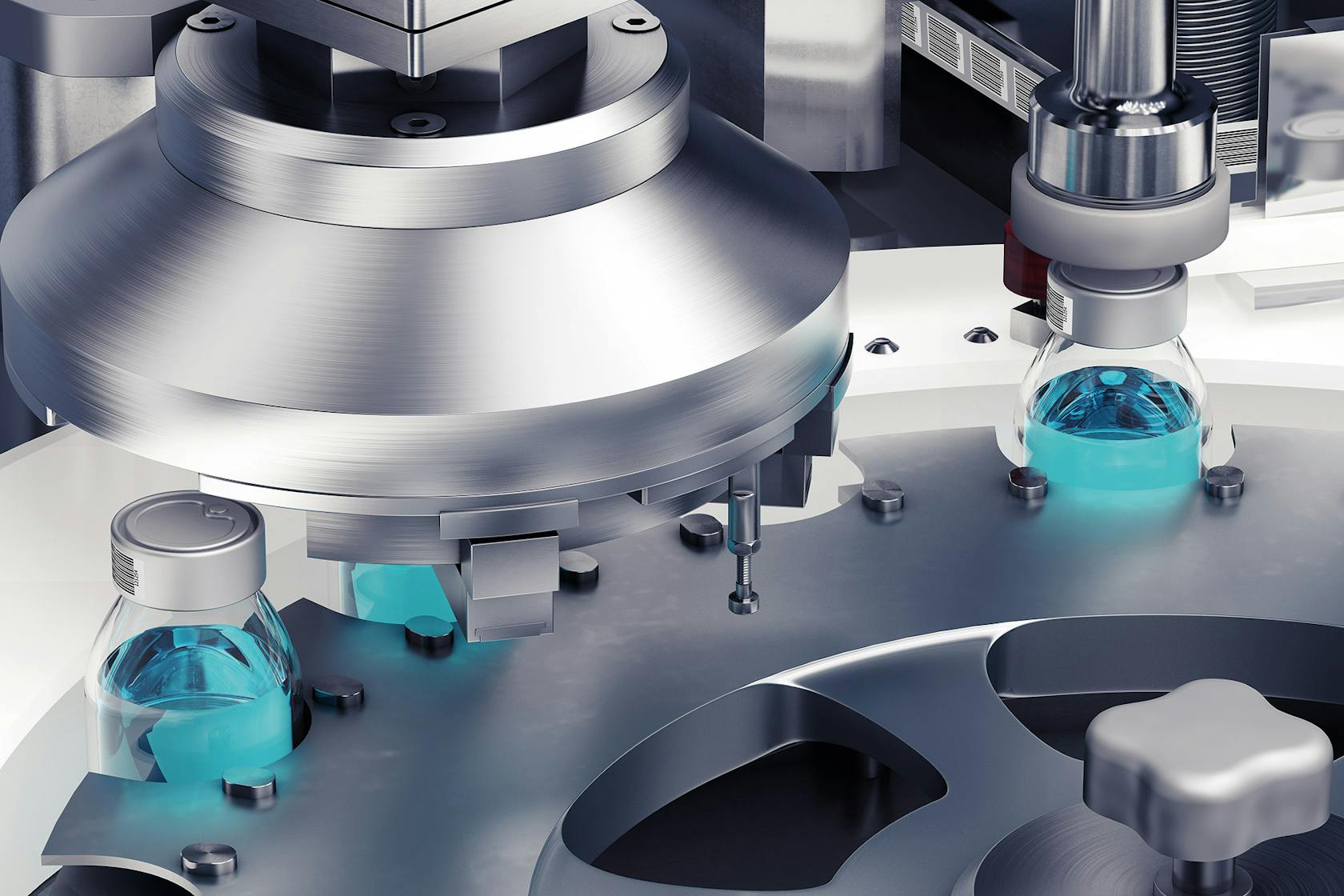
Featured Posts
-
The Truth Behind Jessica Simpsons Snake Sperm Statement
May 11, 2025 -
Bet365 Bonus Code Nypbet Knicks Vs Pistons Series Odds Picks And Preview
May 11, 2025 -
Resi Awards 2025 Winners Announced
May 11, 2025 -
Usmnt Weekend Roundup Dests Return And Pulisics Heroics
May 11, 2025 -
From Serving Passengers To Taking Flight A Former Sia Flight Attendants Journey To Becoming A Pilot
May 11, 2025