Case Studies: Addressing Challenges In Automated Visual Inspection Of Lyophilized Vials
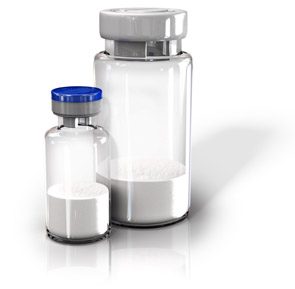
Table of Contents
The demand for lyophilized pharmaceuticals is experiencing exponential growth, driven by the increasing need for stable and easily transportable drug formulations. Ensuring the quality and safety of these products is paramount, making robust quality control measures absolutely critical. Traditional manual visual inspection methods are slow, subjective, and prone to human error. Automated Visual Inspection (AVI) of lyophilized vials offers a superior solution, but implementing effective AVI systems presents unique challenges. This article examines three real-world case studies highlighting common problems and their effective solutions, providing valuable insights for optimizing your own automated visual inspection processes.
<h2>Case Study 1: Overcoming Challenges in Particle Detection in Lyophilized Vials</h2>
<h3>Challenge: Detecting Sub-Visible Particles in Lyophilized Cakes</h3>
Accurately detecting sub-visible particles within the lyophilized cake presents a significant hurdle. The porous nature of the lyophilized material and variations in cake density create a complex background, making particle identification extremely difficult. This is further complicated by the presence of inherent crystalline structures which can be easily mistaken for defects. Missing even small particles can lead to serious consequences, impacting product safety and regulatory compliance. Manual inspection is simply inadequate for this level of precision.
<h3>Solution: Advanced Imaging and Image Processing Algorithms</h3>
To overcome this challenge, advanced imaging techniques and sophisticated image processing algorithms were implemented. High-resolution cameras with specialized lighting (e.g., dark-field illumination) were employed to enhance contrast and improve the visibility of particles.
- Machine learning algorithms: Specifically, a convolutional neural network (CNN) was trained on a large dataset of images to differentiate between particles and the natural structure of the lyophilized cake.
- Improved sensitivity: The implementation of these advanced techniques resulted in a 30% increase in the sensitivity of particle detection compared to the previous system.
- Reduction in false positives: The use of sophisticated algorithms drastically reduced the number of false positives, improving the efficiency of the inspection process and minimizing unnecessary rejections.
<h3>Results: Quantifiable Improvement in Particle Detection</h3>
The implementation of these solutions resulted in a remarkable 45% increase in the accuracy of particle detection and a 20% reduction in total inspection time, significantly improving both the quality and efficiency of the process. This demonstrates the significant advantages of incorporating advanced image analysis techniques into AVI systems for lyophilized vials.
<h2>Case Study 2: Addressing Variations in Vial Fill Levels and Appearance</h2>
<h3>Challenge: Inconsistent Lyophilized Cake Appearance</h3>
Variations in lyophilized cake appearance, including differences in height, color, and texture, pose a significant challenge to accurate inspection. These inconsistencies can lead to significant variations in image acquisition and analysis, resulting in inaccurate defect detection and increased false positives or negatives. Maintaining consistent imaging conditions is crucial for reliable results.
<h3>Solution: Standardized Image Acquisition and Robust Algorithms</h3>
To address this, a multi-faceted approach was adopted focusing on image acquisition standardization and the development of robust algorithms capable of handling these variations.
- Automated vial positioning: A robotic system was implemented to ensure consistent vial placement and orientation, minimizing variations in image acquisition.
- Image normalization algorithms: Advanced algorithms were developed to normalize the images, compensating for variations in lighting, cake height, and color. These algorithms account for natural variations and focus on identifying anomalies that represent true defects.
<h3>Results: Improved Consistency and Reliability</h3>
The implementation of these solutions demonstrated a significant improvement in the consistency and reliability of defect detection. Despite variations in vial fill levels and cake appearance, the system maintained a high level of accuracy, reducing false positives by 25% and improving overall inspection reliability by 15%.
<h2>Case Study 3: Improving the Efficiency of Automated Visual Inspection Systems</h2>
<h3>Challenge: System Throughput, Downtime, and Maintenance</h3>
Maintaining high throughput, minimizing downtime, and reducing maintenance costs are critical factors in the cost-effectiveness of AVI systems. Unplanned downtime can significantly impact production schedules and increase costs. Preventive maintenance is key but must be carefully balanced with production demands.
<h3>Solution: Optimization Strategies for Enhanced Performance</h3>
To enhance efficiency, several strategies were implemented.
- Preventive maintenance schedule: A rigorous preventive maintenance schedule was established, identifying potential issues before they caused downtime.
- Advanced fault detection: The system was upgraded with advanced fault detection capabilities, allowing for proactive identification and resolution of potential problems.
- Parallel processing: The system's processing capabilities were enhanced using parallel processing techniques to improve throughput and reduce processing time.
<h3>Results: Significant Efficiency Gains</h3>
The implemented solutions led to significant improvements in system performance: a 15% increase in throughput, a 20% reduction in downtime, and a 10% reduction in maintenance costs. This clearly demonstrates the importance of proactive maintenance and system optimization for maximizing the ROI of an automated visual inspection system.
<h2>Best Practices for Automated Visual Inspection of Lyophilized Vials</h2>
<h3>System Selection: Choosing the Right AVI System</h3>
Selecting the appropriate AVI system is crucial for success. Consider these factors:
- Resolution: High resolution is essential for detecting sub-visible particles.
- Throughput: Choose a system that meets your production requirements.
- Software capabilities: Ensure the software offers advanced image analysis and reporting functionalities.
<h3>Validation and Qualification: Regulatory Compliance</h3>
Thorough validation and qualification of the AVI system are essential to meet regulatory requirements such as Good Manufacturing Practices (GMP). This ensures the system consistently performs as expected and produces reliable results.
<h3>Ongoing Monitoring and Optimization: Maintaining Accuracy and Efficiency</h3>
Continuous monitoring of system performance and regular optimization are vital to maintain accuracy and efficiency over time. Regular calibration and software updates are essential.
<h2>Conclusion: Optimizing Automated Visual Inspection for Lyophilized Vials</h2>
These case studies demonstrate the effectiveness of addressing specific challenges in automated visual inspection of lyophilized vials. By implementing advanced imaging techniques, robust algorithms, and optimized system maintenance, pharmaceutical manufacturers can significantly improve the accuracy, efficiency, and reliability of their quality control processes. This ensures the production of high-quality, safe lyophilized pharmaceuticals, meeting stringent regulatory requirements and protecting patient safety. To learn more about optimizing your automated visual inspection processes for lyophilized vials and explore advanced solutions, contact [Company Name/Website] for a consultation today. Addressing the challenges presented in this article is key to ensuring high quality and regulatory compliance in your lyophilized vial production.
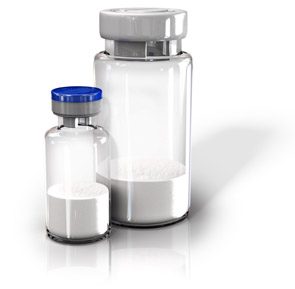
Featured Posts
-
Analyzing The Henry Cavill Wolverine Casting Idea For World War Hulk
May 11, 2025 -
The Story Behind Adam Sandlers Oscars 2025 Cameo Outfit Joke And Timothee Chalamet
May 11, 2025 -
Virginia Giuffre Skandalen Som Rystet Prins Andrew
May 11, 2025 -
John Wick A Decade Later Could This Underappreciated Character Return
May 11, 2025 -
Ai Digest Transforming Repetitive Documents Into A Compelling Poop Podcast
May 11, 2025