Challenges And Solutions In Automated Visual Inspection Of Lyophilized Drug Products
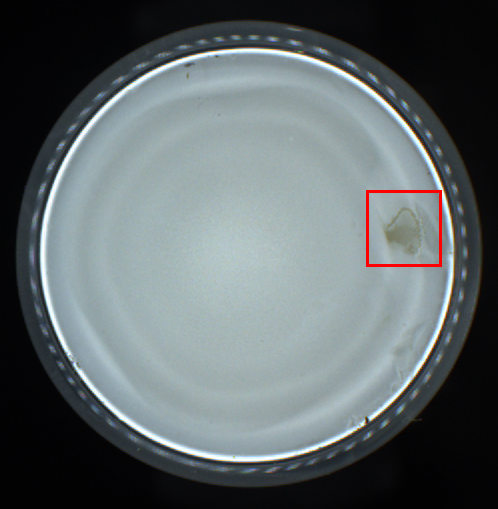
Table of Contents
Challenges in Automated Visual Inspection of Lyophilized Drug Products
The implementation of effective AVI systems for lyophilized drug products presents several significant challenges. These challenges stem from the inherent complexities of lyophilized materials and the stringent quality control requirements of the pharmaceutical industry.
Variability and Complexity of Defects
Lyophilized drug products exhibit a wide range of potential defects, each presenting unique challenges for automated detection. These defects vary significantly in appearance and size, making consistent identification difficult.
- Cracks: These can range from hairline fractures to significant fissures, impacting the integrity of the product.
- Collapse: Partial or complete collapse of the lyophilized cake alters its appearance and potentially its stability.
- Particulate Matter: Foreign particles within or on the lyophilized cake are a critical quality concern.
- Discoloration: Subtle changes in color can indicate degradation or inconsistencies in the manufacturing process.
Differentiating between acceptable variations in appearance and critical defects is a major hurdle. Furthermore, changes in formulation or manufacturing processes can significantly alter the appearance of defects, requiring constant algorithm recalibration and adjustments for robust defect detection.
Lighting and Imaging Challenges
The translucent nature of lyophilized cakes and the use of glass or plastic vials create significant challenges for image acquisition. The inherent properties of the material and container often lead to issues with image clarity and accurate defect detection.
- Glare and Reflections: Light reflecting off the vial surface or the lyophilized cake can mask defects, hindering accurate assessment.
- Shadowing: Uneven lighting can create shadows that obscure defects or create artificial ones.
Advanced lighting techniques, such as structured light and polarized light, are being employed to mitigate these issues. However, the optimal lighting strategy often depends on the vial material, shape, and the specific characteristics of the lyophilized product, making standardization a complex undertaking.
High Throughput Requirements
Pharmaceutical manufacturing demands high-speed inspection to maintain production efficiency. Balancing speed and accuracy in automated systems is crucial.
- Throughput Limitations: Current AVI technologies may struggle to keep pace with high-volume production lines.
- Bottlenecks: Slow inspection speeds can create bottlenecks in the overall manufacturing process, impacting productivity and cost-effectiveness.
- Integration Challenges: Seamless integration with existing production lines and other quality control systems is vital for efficient implementation.
Solutions and Technological Advancements
Addressing the challenges discussed above requires innovative solutions that leverage advanced imaging techniques, sophisticated algorithms, and improved system design.
Advanced Imaging Techniques
Moving beyond traditional 2D imaging, advanced techniques significantly enhance defect detection capabilities.
- Hyperspectral Imaging: This technique captures spectral information across a wide range of wavelengths, providing detailed chemical and physical information about the lyophilized cake. This allows for the identification of subtle defects invisible to standard imaging.
- Multispectral Imaging: Similar to hyperspectral imaging, but utilizing a smaller number of wavelengths, it offers a cost-effective alternative.
- 3D Imaging: Provides a three-dimensional representation of the lyophilized cake, enabling the detection of defects that might be missed using traditional 2D imaging. This is especially useful in identifying cracks or collapses that have depth.
Each technique offers unique advantages and limitations depending on the specific application and the nature of the defects being detected.
Artificial Intelligence and Machine Learning
AI and machine learning (ML) play a crucial role in enhancing the accuracy and efficiency of automated visual inspection.
- Deep Learning Algorithms: These algorithms are trained on large datasets of images containing various defects, enabling them to learn to identify and classify defects with high accuracy.
- Improved Accuracy: AI-powered systems consistently outperform traditional rule-based systems in identifying subtle defects.
- Reduced False Positives: AI algorithms can be trained to minimize false positive identifications, reducing unnecessary intervention and improving overall efficiency.
Data acquisition and model training are significant challenges, however, requiring high-quality, representative datasets and specialized expertise.
Improved System Design and Integration
Advancements in robotics and automation are pivotal in improving the throughput and reliability of AVI systems.
- Robotic Systems: Automated robotic systems handle the precise movement and positioning of vials, facilitating high-speed inspection.
- Seamless Integration: Efficient integration with existing manufacturing execution systems (MES) and enterprise resource planning (ERP) systems is critical for streamlined data management and overall process efficiency.
- Validation and Compliance: Rigorous validation and adherence to regulatory requirements are essential for ensuring the reliability and acceptance of AVI systems in the pharmaceutical industry.
Conclusion: The Future of Automated Visual Inspection of Lyophilized Drug Products
Addressing the challenges in Automated Visual Inspection of Lyophilized Drug Products requires a multi-pronged approach, incorporating advanced imaging techniques, powerful AI algorithms, and robust system design. The ongoing development of these technologies promises to significantly enhance the efficiency and accuracy of AVI, leading to improved quality control and enhanced patient safety. Investing in advanced automated visual inspection systems is crucial for maintaining high-quality standards in the production of lyophilized drugs. Explore the latest technologies and solutions to optimize your quality control processes and ensure patient safety.
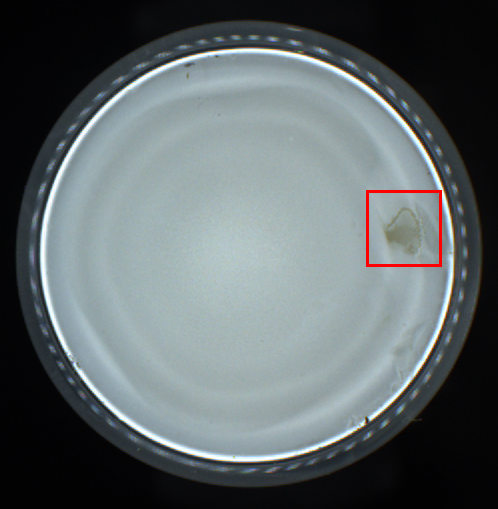
Featured Posts
-
Revelation Mask Singer 2025 L Autruche Une Celebrite Connue De Chantal Ladesou Et Laurent Ruquier
May 11, 2025 -
Boston Celtics Player Skips Nba Award Nomination Push
May 11, 2025 -
L Avis Sans Filtre De Chantal Ladesou Sur Ines Reg Mask Singer
May 11, 2025 -
Behind The Scenes Of The Stallone Parton Musical Comedy That Never Took Off
May 11, 2025 -
Nba Betting Cavaliers Vs Knicks Odds Predictions And Best Bets February 21st
May 11, 2025