Ensuring Quality Control: Addressing Challenges In Automated Lyophilized Vial Inspection
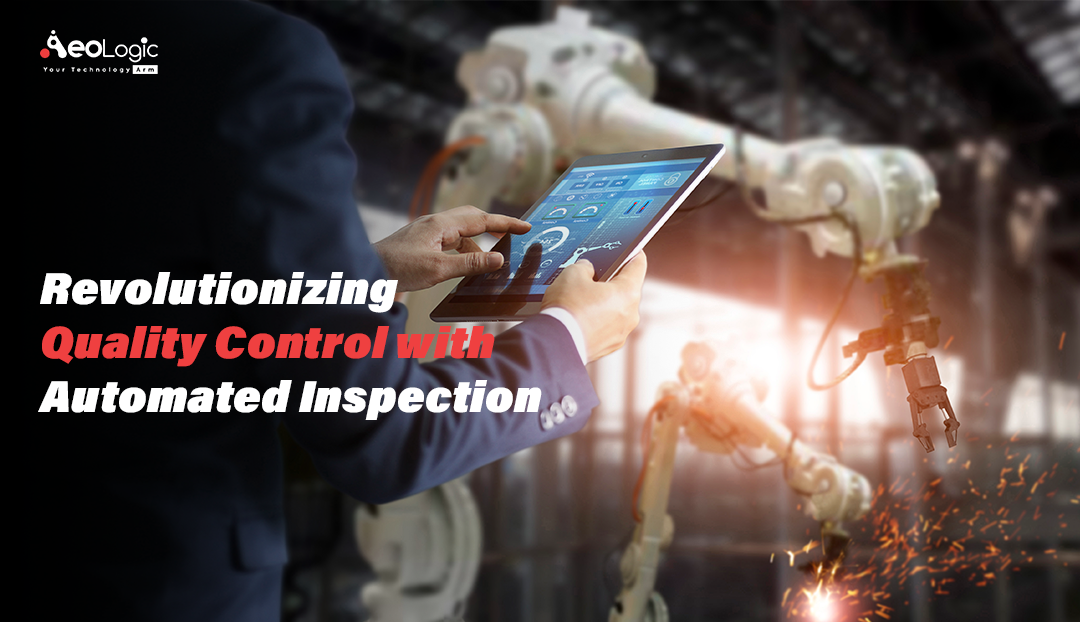
Table of Contents
Image Acquisition and Processing Challenges
Automated lyophilized vial inspection hinges on accurate image analysis. However, achieving this accuracy presents significant hurdles. The inherent variability in lyophilized vials, coupled with the complexities of image processing, necessitates sophisticated solutions.
Variations in Vial Appearance
Lyophilized vials exhibit considerable visual inconsistencies stemming from factors like cake formation, residual moisture content, and fill volume variations. These variations directly impact the accuracy of automated inspection systems.
- Inconsistent lighting: Uneven lighting conditions can lead to misinterpretations of cake characteristics, such as its density and homogeneity. Advanced lighting techniques, like multi-spectral imaging, can mitigate this issue.
- Variations in vial material and color: Differences in glass type, color, and clarity can complicate image segmentation, making it difficult for algorithms to isolate the lyophilized cake from the vial itself. Pre-processing techniques that account for these variations are crucial.
- Subtle defects: Small cracks, particulate matter, or inconsistencies in the lyophilized cake can be easily missed by algorithms if they are not specifically trained to detect these subtle defects. This necessitates the use of high-resolution imaging and robust algorithms with high sensitivity.
Developing Robust Algorithms
Developing algorithms capable of reliably identifying defects within the inherent variability of lyophilized vials requires sophisticated image processing and machine learning techniques.
- Machine learning (ML) and deep learning (DL): These advanced algorithms offer the potential for significantly improved defect detection. DL models, in particular, can learn to identify subtle defects from large training datasets, even in the presence of significant background variations.
- Regular algorithm updates and retraining: As production processes evolve and new defect types emerge, regular retraining of the algorithms with updated datasets is crucial for maintaining accuracy and preventing false positives or negatives.
- Careful consideration of image acquisition parameters: The choice of lighting, resolution, and other image acquisition parameters directly impacts algorithm performance. Optimization of these parameters is critical for achieving optimal results.
Integration and System Validation
Successfully implementing automated lyophilized vial inspection requires more than just acquiring the equipment; seamless integration with existing processes and rigorous validation are essential.
System Integration with Existing Processes
Integrating automated inspection systems into existing production lines demands careful planning to ensure efficiency and avoid disrupting workflow.
- Compatibility with material handling systems: The automated system must integrate smoothly with existing conveyor systems, robotics, and other equipment to ensure a continuous workflow.
- Data management and integration with existing QC databases: The system should seamlessly integrate with existing quality control databases to allow for efficient data tracking, analysis, and reporting.
- Validation and qualification: The integrated system must undergo thorough validation and qualification to meet regulatory requirements, demonstrating its performance and reliability within the specific production environment.
Validation and Regulatory Compliance
Thorough validation is paramount to demonstrate the accuracy and reliability of the automated lyophilized vial inspection system, ensuring compliance with regulatory standards such as FDA 21 CFR Part 11.
- IQ/OQ/PQ protocols: A comprehensive validation plan encompassing Installation Qualification (IQ), Operational Qualification (OQ), and Performance Qualification (PQ) is essential.
- Defect detection sensitivity: The system's ability to accurately detect defects at pre-defined sensitivity levels must be rigorously demonstrated and documented.
- Data integrity and audit trail: Maintaining data integrity and a complete audit trail is crucial for compliance and traceability.
Cost and Return on Investment (ROI)
While the initial investment in automated lyophilized vial inspection can be significant, the long-term benefits justify the cost in terms of improved quality and efficiency.
Initial Investment Costs
The upfront cost of purchasing and implementing an automated lyophilized vial inspection system can be substantial. A thorough cost-benefit analysis is crucial before making a decision.
- Equipment costs: This includes the cost of the inspection equipment itself, software licenses, and integration services.
- Personnel training and ongoing maintenance: Training personnel on the system's operation and maintenance is vital, along with budgeting for ongoing maintenance and potential repairs.
Long-term Benefits and ROI
Despite the high initial investment, automated inspection offers significant long-term benefits that contribute to a positive ROI.
- Improved product quality: Reduced defect rates lead to higher quality products and fewer recalls.
- Increased throughput and production efficiency: Automated systems can process vials much faster than manual inspection, improving overall production efficiency.
- Reduced labor costs and improved worker safety: Automation reduces the need for manual labor, lowering labor costs while simultaneously improving worker safety by eliminating repetitive strain injuries.
Conclusion
Automated lyophilized vial inspection offers a significant advancement in quality control for pharmaceutical manufacturing. However, overcoming the challenges related to image acquisition, system integration, and validation is critical for successful implementation. By addressing these issues proactively and strategically investing in robust systems and training, manufacturers can significantly enhance product quality, reduce costs, and improve compliance with regulatory requirements. Implementing a well-validated automated lyophilized vial inspection system is key to maintaining the highest standards of quality in pharmaceutical production. Contact us today to discuss your automated lyophilized vial inspection needs and explore solutions to enhance your quality control processes.
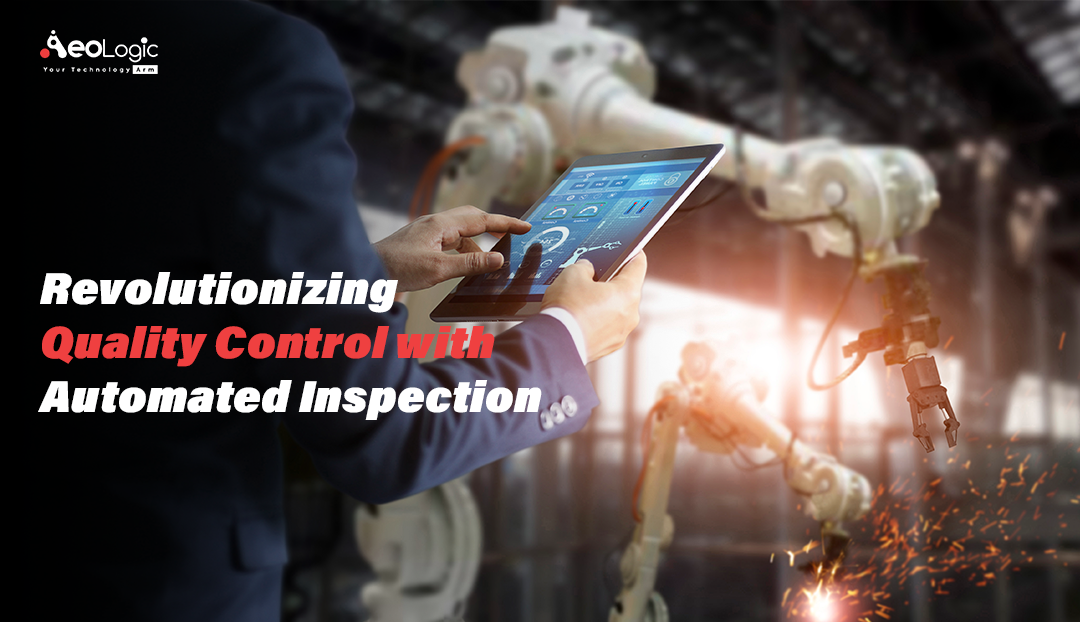
Featured Posts
-
From Bellator To Ufc Manon Fiorots Rise After Her Only Loss
May 12, 2025 -
Early Season Mlb Power Comparing Chisholm And Judges Statistics
May 12, 2025 -
Zuckerbergs Testimony Highlights Instagrams Fight Against Tik Tok Dominance
May 12, 2025 -
Boris Dzhonson Rezko Kritikuet Mirniy Plan Trampa
May 12, 2025 -
Shop The 2025 New York Yankees Collection Hats Jerseys And More
May 12, 2025
Latest Posts
-
I Fonitiki Roytina Tis Tzesika Simpson Ena Amfilegomeno Mystiko
May 12, 2025 -
Tzesika Simpson I Alitheia Piso Apo Tis Fimes Gia Ti Foni Tis
May 12, 2025 -
Luxury Living Notable Homes Showcased On Mtv Cribs
May 12, 2025 -
I Foni Tis Tzesika Simpson Mythos I Pragmatikotita I Methodos Me To Fidisio Sperma
May 12, 2025 -
New Music From Jessica Simpson Thanks To Eric Johnsons Support
May 12, 2025