Improving Automated Visual Inspection For Lyophilized Vials: A Practical Guide
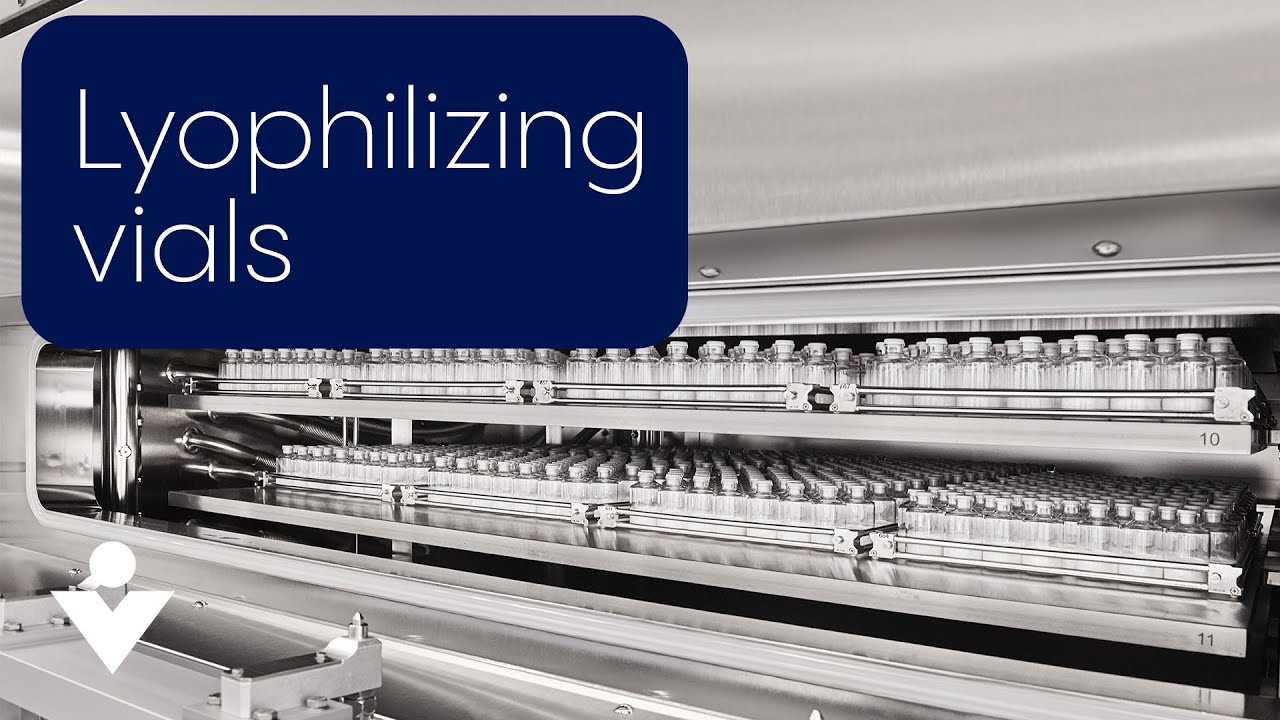
Table of Contents
Enhancing Image Acquisition for Lyophilized Vials
High-quality image acquisition forms the bedrock of effective automated visual inspection. Suboptimal images lead to inaccurate defect detection, compromising the entire process. Two critical aspects need careful consideration: lighting and camera settings, and handling variations in vial appearance.
Optimizing Lighting and Camera Settings
Proper lighting is crucial for minimizing glare and shadows, enabling the system to accurately identify defects. Different lighting techniques offer advantages depending on the vial type and the nature of the defects being sought.
- Diffuse lighting: Provides even illumination, minimizing harsh shadows and reflections. Ideal for detecting surface imperfections.
- Coaxial lighting: Illuminates the vial from directly above, highlighting subtle surface variations and minimizing reflections. Effective for detecting particulate matter.
- Backlighting: Useful for detecting inconsistencies in fill levels and the presence of air bubbles.
Camera settings must be carefully calibrated to capture clear, detailed images. Factors to consider include:
- Resolution: Higher resolution leads to better defect detection but increases processing time. The optimal resolution depends on the size and type of defects being inspected.
- Exposure time: Adjusts the amount of light reaching the sensor, crucial for balancing brightness and minimizing noise.
- Gain: Amplifies the signal from the sensor, improving sensitivity but potentially increasing noise. Careful optimization is crucial.
Regular calibration and maintenance of the entire imaging system are paramount for consistent performance and accurate results.
Handling Variations in Vial Appearance
Lyophilized vials present unique challenges due to variations in color, fill levels, and the inherent characteristics of the lyophilized product itself. These variations can significantly impact image processing and defect detection. To overcome this, sophisticated image processing techniques are essential:
- Image normalization: Adjusts for variations in lighting and background intensity, ensuring consistent image brightness and contrast across all vials.
- Background subtraction: Removes the background from the image, isolating the vial and facilitating easier defect identification.
- Advanced algorithms: Robust algorithms are required to handle the natural variations in lyophilized products and still reliably identify defects. These may include techniques like adaptive thresholding and morphological operations.
Advanced Image Processing Techniques for Defect Detection
Traditional image processing techniques often fall short in detecting subtle defects or handling the complexities of lyophilized vials. The integration of AI and machine learning significantly enhances the accuracy and reliability of automated visual inspection.
Implementing AI and Machine Learning
AI and ML algorithms offer unparalleled capabilities in defect detection. Convolutional Neural Networks (CNNs) are particularly well-suited for image analysis, excelling at identifying patterns and variations indicative of defects.
- CNNs: These algorithms can learn to recognize complex patterns associated with specific defects, adapting to variations in vial appearance and improving detection accuracy over time.
- Self-learning algorithms: These algorithms continuously learn and adapt as they process more data, improving their ability to detect new and emerging defects. This is crucial for maintaining high accuracy in dynamic production environments.
- Advantages over traditional methods: AI/ML offer superior accuracy, reduced false positives and negatives, and the ability to handle complex variations in vial appearance.
Improving Defect Classification and Reporting
Accurate classification and reporting of detected defects are critical for maintaining product quality and regulatory compliance. The system needs to provide clear, concise information about the type, location, and severity of each defect.
- Reducing false positives/negatives: Careful algorithm tuning and validation are crucial to minimize these errors. Data analysis can identify sources of error and inform improvements to the system.
- Clear reporting and documentation: The system should generate comprehensive reports documenting all detected defects, including images and relevant metadata. This is essential for traceability and regulatory compliance.
- Integration with quality management systems: Seamless integration with existing quality management systems streamlines data management and analysis. Tracking defect trends over time can help pinpoint areas for process improvement.
Validating and Qualifying Automated Visual Inspection Systems
Validation and qualification are crucial for ensuring the system meets the required performance standards and regulatory requirements. This involves establishing performance metrics and demonstrating regulatory compliance.
Establishing Performance Metrics
Key performance indicators (KPIs) are essential for objectively assessing the system's performance. These metrics provide a quantitative measure of the system's ability to detect defects accurately and reliably.
- Sensitivity: The ability of the system to correctly identify true defects.
- Specificity: The ability of the system to correctly identify true negatives (absence of defects).
- Accuracy: An overall measure combining sensitivity and specificity.
- Acceptance criteria: Pre-defined thresholds for acceptable performance levels based on risk assessment and regulatory requirements.
Regular performance reports using these KPIs ensure the system continues to meet the established standards.
Regulatory Compliance and Documentation
Compliance with relevant regulations, such as 21 CFR Part 11 in the US, is mandatory for automated visual inspection systems in the pharmaceutical industry.
- Data integrity: Ensuring the accuracy, completeness, and consistency of all data generated by the system.
- Audit trails: Maintaining detailed records of all system activities, including user actions, data modifications, and system events.
- User access control: Implementing secure access controls to protect data integrity and prevent unauthorized modifications.
- Thorough documentation: Maintaining comprehensive documentation throughout the validation process, including test protocols, results, and reports. Failure to meet regulatory requirements can lead to significant penalties and product recalls.
Conclusion
Implementing robust Automated Visual Inspection for Lyophilized Vials, leveraging advanced image processing techniques like AI/ML and adhering to rigorous validation procedures, significantly enhances quality control in lyophilized vial production. By optimizing lighting and camera settings, handling variations in vial appearance, and establishing clear performance metrics, manufacturers can achieve higher accuracy, efficiency, and regulatory compliance. To achieve superior results and stay ahead in the pharmaceutical industry, consider optimizing Automated Visual Inspection processes now. Invest in upgrading your systems to incorporate these best practices and ensure the production of high-quality lyophilized vials. Embrace advanced Automated Visual Inspection techniques and ensure your products consistently meet the highest standards of quality.
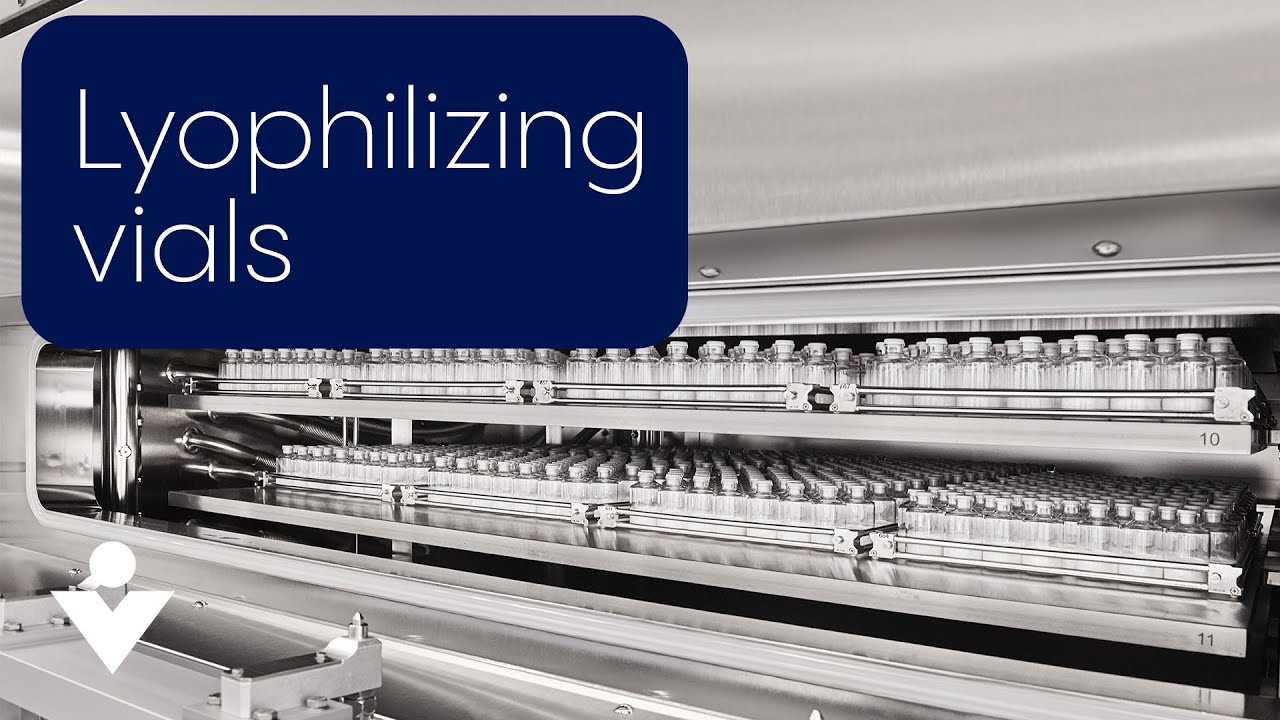
Featured Posts
-
Eric Antoine Un Bebe Avec Sa Nouvelle Compagne Apres La Separation
May 11, 2025 -
Payton Pritchards Childhood Connection A Career Milestone Made More Meaningful
May 11, 2025 -
Un Omagiu Meritat Thomas Mueller Si Ultima Sa Aparitie Pe Teren
May 11, 2025 -
The Hotel Transylvania Universe Movies Shows And Games
May 11, 2025 -
Le Divorce D Eric Antoine Et L Arrivee D Un Nouveau Bebe
May 11, 2025