Improving The Accuracy Of Automated Visual Inspection For Lyophilized Vials
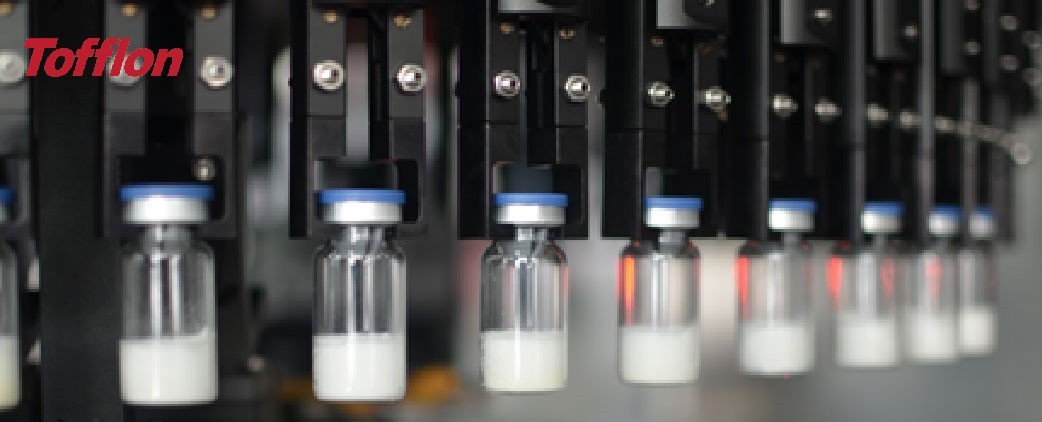
Table of Contents
Optimizing Image Acquisition for Lyophilized Vial Inspection
Effective image acquisition is paramount for accurate automated visual inspection. Poor image quality directly impacts the ability of algorithms to detect defects. Two crucial aspects to optimize are lighting and camera selection.
Lighting and Illumination Techniques
Appropriate lighting is essential for minimizing shadows and reflections, ensuring clear image capture of even subtle defects. Several strategies can significantly improve image quality:
- Coaxial lighting: Provides even illumination by directing light parallel to the optical axis, minimizing shadows. Ideal for detecting surface defects.
- Diffuse lighting: Soft, diffused light minimizes harsh shadows and reflections, suitable for revealing cracks or inconsistencies in fill level.
- Ring lighting: Offers uniform illumination around the vial, excellent for detecting particulate matter and other defects.
- Specialized filters: Utilizing filters like polarizers can further reduce glare and enhance contrast, making defects more readily apparent.
Careful selection of light intensity is crucial. Overexposure washes out details, while underexposure obscures defects. Precise control and adjustment are vital for optimal performance.
Camera Selection and Resolution
High-resolution cameras are critical for capturing fine details on lyophilized vials. The choice of sensor type and resolution directly impacts defect detection capabilities:
- Resolution requirements: Higher resolution (e.g., megapixels) is necessary to detect smaller defects like micro-cracks or minute particulate matter.
- Camera speed and throughput: Faster cameras are essential for high-throughput manufacturing, ensuring minimal downtime.
- Specialized lenses: Macro lenses provide the magnification needed to resolve small defects, capturing sharp images with high clarity. Choosing the correct lens is critical to the overall effectiveness of the inspection.
Advanced Image Processing Algorithms for Defect Detection
Sophisticated image processing algorithms are fundamental to accurate defect detection. Modern techniques, such as machine learning and AI, are revolutionizing the field.
Machine Learning and AI in Visual Inspection
Machine learning, specifically convolutional neural networks (CNNs), offers significant advantages:
- Training datasets: Large, well-annotated datasets of lyophilized vials with various defects are necessary to train effective AI models.
- Adaptability: AI-powered systems can adapt to variations in vial appearance, such as variations in fill level or slight inconsistencies in the lyophilization process.
- Subtle defect detection: Deep learning algorithms excel at detecting subtle defects that may be easily missed by human inspectors or simpler algorithms.
Image Enhancement and Filtering Techniques
Image enhancement techniques further refine the images for optimal defect detection:
- Noise reduction: Reduces image noise, improving the clarity of details.
- Edge detection: Highlights the boundaries of defects, making them easier to identify.
- Contrast enhancement: Increases the difference in brightness between defects and their surroundings, improving visibility.
- Image segmentation: Isolates potential defects from the background for precise analysis, improving the accuracy of defect classification.
Calibration and Validation of Automated Inspection Systems
Regular calibration and validation are crucial for maintaining the accuracy and reliability of automated visual inspection systems.
Regular Calibration Procedures
Calibration ensures the system consistently meets predefined accuracy standards:
- Calibration standards: Utilizing certified reference standards with known defects allows for precise calibration.
- Calibration frequency: The frequency depends on system usage and regulatory requirements. More frequent calibration is generally recommended for high-volume production lines.
- Documentation and record-keeping: Meticulous documentation of calibration procedures and results is essential for regulatory compliance.
Validation and Performance Verification
Validation verifies the system's ability to accurately detect defects:
- Performance qualification (PQ) testing: Demonstrates the system meets performance specifications under real-world operating conditions.
- Known defect samples: Testing with vials containing known defects of varying sizes and types assesses detection rates.
- Performance reports: Regular performance reports track the system's accuracy over time, identifying potential issues before they impact production.
Achieving Optimal Accuracy in Automated Visual Inspection of Lyophilized Vials
Improving the accuracy of automated visual inspection for lyophilized vials requires a multifaceted approach. Optimizing image acquisition through careful lighting and camera selection, leveraging advanced image processing algorithms like machine learning, and implementing rigorous calibration and validation procedures are all critical. Accurate automated visual inspection increases efficiency, minimizes human error, improves product quality, and ensures regulatory compliance. By implementing these strategies, manufacturers can significantly enhance the accuracy and reliability of their automated visual inspection processes, ensuring the highest quality standards for their pharmaceutical products. Invest in improving your automated visual inspection systems today – your product quality and regulatory compliance depend on it.
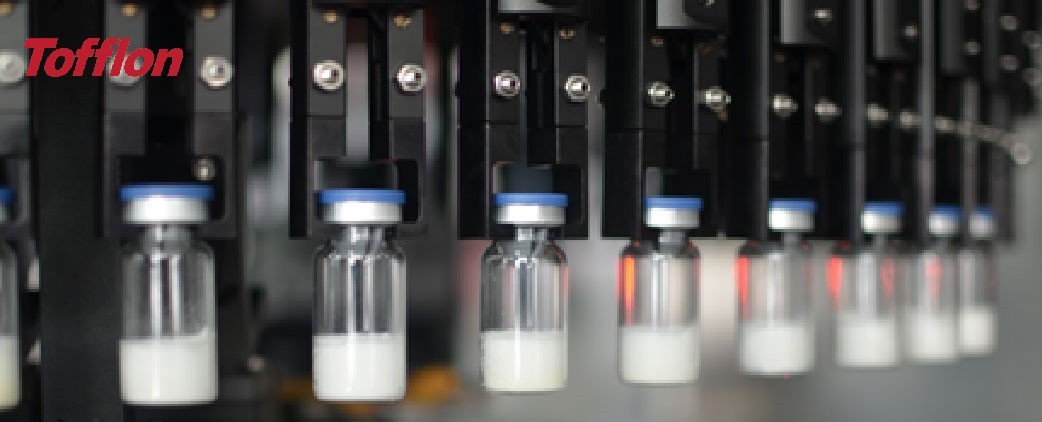
Featured Posts
-
New York Knicks 37 Point Loss Prompts Thibodeaus Call For More Determination
May 12, 2025 -
Zurich Classic Mc Ilroy And Lowry Six Strokes Behind
May 12, 2025 -
Confirmed Crazy Rich Asians Series Coming To Max
May 12, 2025 -
Ufc 315 Fight Card Belal Muhammad Vs Jack Della Maddalena Prediction And Betting Preview
May 12, 2025 -
Increased Risk For Indy 500 Drivers In 2025
May 12, 2025
Latest Posts
-
I Fonitiki Roytina Tis Tzesika Simpson Ena Amfilegomeno Mystiko
May 12, 2025 -
Tzesika Simpson I Alitheia Piso Apo Tis Fimes Gia Ti Foni Tis
May 12, 2025 -
Luxury Living Notable Homes Showcased On Mtv Cribs
May 12, 2025 -
I Foni Tis Tzesika Simpson Mythos I Pragmatikotita I Methodos Me To Fidisio Sperma
May 12, 2025 -
New Music From Jessica Simpson Thanks To Eric Johnsons Support
May 12, 2025