Overcoming Hurdles In Automated Visual Inspection Of Lyophilized Drug Products
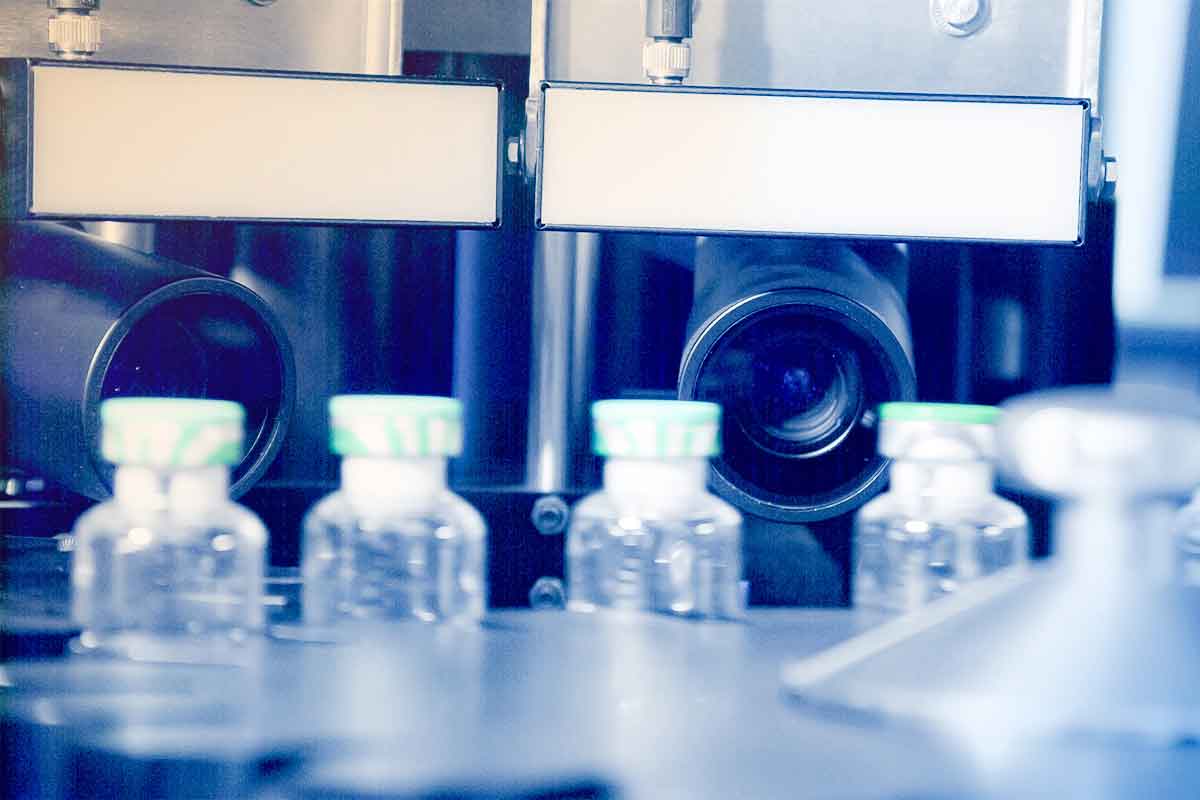
Table of Contents
Challenges in Image Acquisition and Preprocessing for Lyophilized Products
The successful implementation of automated visual inspection of lyophilized drug products hinges on the ability to acquire high-quality images that accurately represent the product's condition. However, several factors complicate this process.
Variations in Lyophilized Product Appearance
Lyophilized products exhibit inherent variability in appearance. Cake collapse, cracks, surface imperfections, and variations in color are common, significantly impacting the accuracy and reliability of automated visual inspection systems. These variations can lead to misinterpretations by the automated system, resulting in false positives or false negatives.
- Impact: Inconsistent image analysis due to the diverse appearances of lyophilized products.
- Solutions:
- Employ advanced imaging techniques like multispectral or hyperspectral imaging to capture more detailed information about the product's surface.
- Optimize lighting conditions using controlled illumination and minimize shadowing.
- Implement sophisticated image preprocessing algorithms to normalize variations in brightness, contrast, and color.
Dealing with Glare and Reflections
Glare and reflections on the vial surfaces are a common problem, obscuring defects and hindering accurate analysis by automated visual inspection systems. The curved surfaces of vials can act as lenses, magnifying and distorting light sources.
- Impact: Masks defects, leading to false negatives in automated visual inspection of lyophilized drug products.
- Solutions:
- Utilize anti-reflective coatings on vials to minimize glare.
- Employ optimized lighting angles to reduce reflections.
- Implement image processing techniques, such as polarization filtering, to remove or reduce glare from the images.
Accurate Color Calibration and Consistency
Maintaining color consistency across different batches and inspection systems is crucial for accurate defect detection in automated visual inspection of lyophilized drug products. Slight variations in color can be indicative of defects. Maintaining color uniformity in imaging is paramount.
- Impact: Color variations can lead to misidentification of defects or false positives.
- Solutions:
- Establish rigorous color calibration procedures using standardized color charts.
- Maintain standardized lighting conditions throughout the inspection process.
- Utilize colorimetric analysis techniques to quantify and correct color variations.
Developing Robust Defect Detection Algorithms
The development of robust defect detection algorithms is critical for the success of automated visual inspection of lyophilized drug products. These algorithms must be capable of identifying subtle defects that may be easily missed by human inspectors.
Algorithms for Detecting Subtle Defects
Detecting subtle defects such as micro-cracks, small discolorations, and minute irregularities requires advanced algorithms that can analyze complex image data.
- Challenges: Subtle defects present significant challenges for traditional image processing techniques.
- Solutions:
- Implement machine learning (ML) and deep learning (DL) approaches, specifically convolutional neural networks (CNNs), to learn complex patterns and identify subtle defects.
- Utilize support vector machines (SVMs) for classification of defects based on extracted features.
Addressing False Positives and False Negatives
Minimizing both false positives (incorrectly identifying defects) and false negatives (missing actual defects) is paramount for ensuring the reliability of automated visual inspection systems. High false positive rates can lead to unnecessary product rejection, while high false negative rates can result in defective products reaching the market.
- Impact: Inaccurate results impacting product quality and regulatory compliance.
- Solutions:
- Employ data augmentation techniques to increase the size and diversity of the training dataset.
- Regularly retrain the models using updated data to improve accuracy and reduce errors.
Algorithm Validation and Qualification
Regulatory agencies require rigorous validation and qualification of automated visual inspection algorithms. This process ensures that the algorithms meet the required performance standards and are suitable for their intended use.
- Importance: Meeting regulatory requirements (e.g., FDA 21 CFR Part 11) for automated visual inspection.
- Solutions:
- Conduct thorough testing to demonstrate the accuracy and reliability of the algorithms.
- Maintain comprehensive documentation of the validation process.
Integration and Validation within the Manufacturing Process
Successful implementation of automated visual inspection of lyophilized drug products requires seamless integration with existing manufacturing processes and quality control systems.
Seamless Integration with Existing Systems
Integration with existing production lines and quality control systems must be straightforward to avoid disrupting workflows.
- Importance: Efficient integration to minimize disruption to the production line.
- Solutions:
- Select AVI systems designed for easy integration with existing infrastructure.
- Develop appropriate interfaces to ensure data exchange between systems.
Data Management and Reporting
Automated visual inspection systems generate vast amounts of data, necessitating robust data management systems. Clear and informative reporting is essential for effective quality control.
- Importance: Efficient data storage, retrieval, and analysis are crucial.
- Solutions:
- Implement a dedicated database to store and manage inspection data.
- Develop reporting tools to generate comprehensive reports on inspection results.
Regulatory Compliance and Validation
Compliance with regulatory requirements, such as FDA 21 CFR Part 11, is essential for automated visual inspection systems in the pharmaceutical industry.
- Importance: Meeting regulatory requirements for data integrity and audit trails.
- Solutions:
- Select systems validated for compliance with relevant regulations.
- Implement robust validation protocols to ensure ongoing compliance.
Conclusion: Overcoming the Hurdles in Automated Visual Inspection of Lyophilized Drug Products
Implementing effective automated visual inspection of lyophilized drug products requires addressing several significant challenges. These include variations in product appearance, glare and reflections, color calibration inconsistencies, developing robust defect detection algorithms, and ensuring seamless integration with existing systems. By employing advanced imaging techniques, sophisticated algorithms, and rigorous validation procedures, pharmaceutical manufacturers can overcome these hurdles. Addressing false positives and negatives remains crucial for accurate and reliable defect detection. By implementing these strategies and investing in advanced automated visual inspection solutions, pharmaceutical manufacturers can significantly improve the quality and safety of their lyophilized drug products, ensuring regulatory compliance and patient safety.
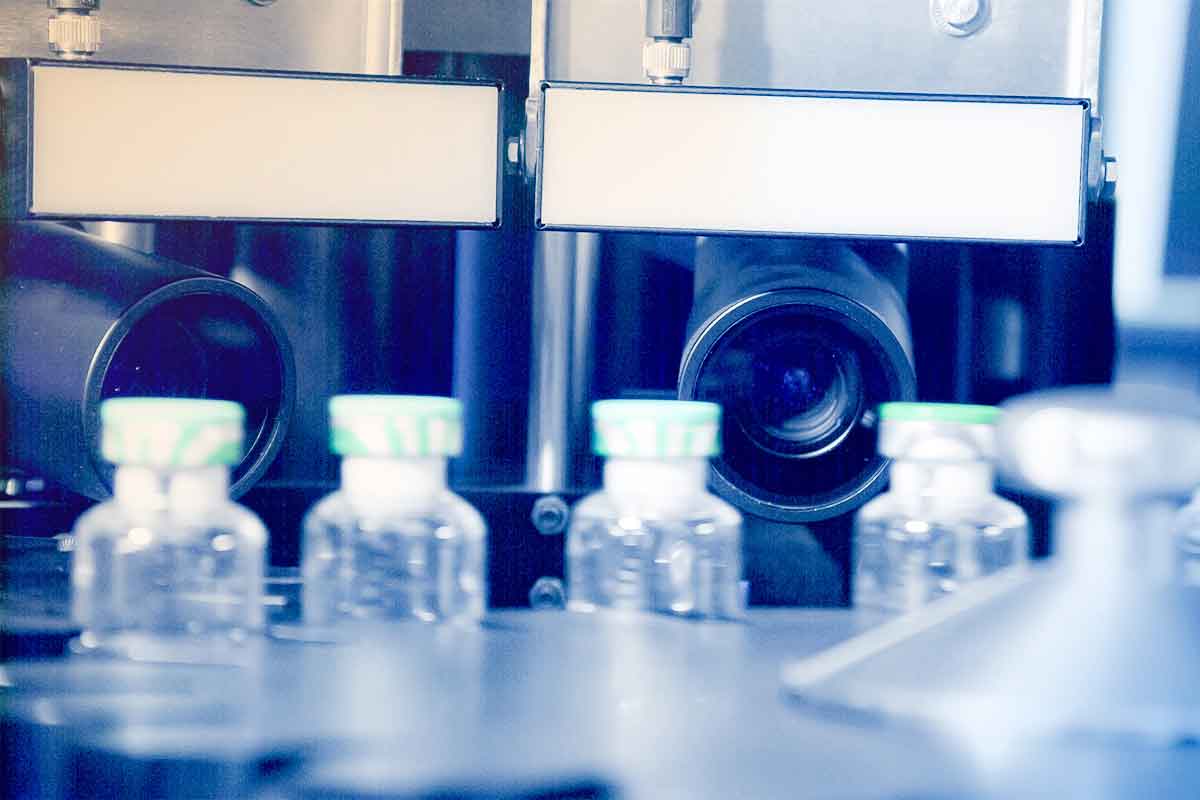
Featured Posts
-
Nba Awards 2024 Payton Pritchards Sixth Man Of The Year Win
May 12, 2025 -
Kritika Dzhonsona Chi Realniy Mirniy Plan Trampa Dlya Ukrayini
May 12, 2025 -
Jurickson Profars Ped Suspension Implications For His Career
May 12, 2025 -
Lily Collins And Charlie Mc Dowell A Glimpse Into Family Life With Daughter Tove
May 12, 2025 -
Analyzing Aaron Judges Hall Of Fame Chances At The 1 000 Game Milestone
May 12, 2025
Latest Posts
-
Jessica Simpsons Controversial Snake Sperm Remarks A Deep Dive
May 12, 2025 -
B And W Trailer Hitches Heavy Hitters All Star Event 100 K Bass Fishing Tournament At Smith Mountain Lake
May 12, 2025 -
I Fonitiki Roytina Tis Tzesika Simpson Ena Amfilegomeno Mystiko
May 12, 2025 -
Tzesika Simpson I Alitheia Piso Apo Tis Fimes Gia Ti Foni Tis
May 12, 2025 -
Luxury Living Notable Homes Showcased On Mtv Cribs
May 12, 2025