Overcoming The Challenges: Robotic Automation In Nike Sneaker Factories
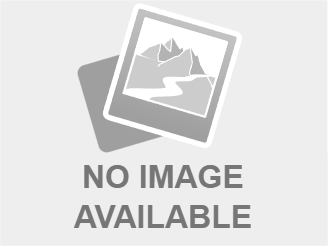
Table of Contents
The High Initial Investment Costs of Robotic Systems
Implementing robotic systems in sneaker factories requires substantial upfront investment. This is a significant challenge for even a large corporation like Nike. The high capital expenditure can be daunting, making careful planning and strategic financial decisions crucial.
- High capital expenditure: The cost of purchasing and installing advanced robotic systems, including robots, sophisticated software, integration hardware, and specialized tooling, is extremely high. This includes the cost of integrating the robots with existing manufacturing equipment and infrastructure.
- Return on Investment (ROI): Calculating a clear and swift ROI can be challenging. Factors like downtime during integration, the cost of retraining employees, and the potential for unforeseen technical issues all need to be considered. A longer-term perspective is often necessary to fully realize the benefits of automation.
- Funding options and strategic planning: Nike needs to explore various funding options to mitigate financial risks. This includes securing loans, exploring venture capital partnerships, and leveraging government incentives designed to encourage automation in manufacturing. A well-defined strategic plan outlining implementation phases, cost projections, and ROI targets is essential.
- Example: The cost of a single advanced robotic arm capable of precise assembly, such as attaching the sole to the upper of a sneaker, can easily exceed $50,000, and this doesn't include the cost of the supporting software and integration. A complete robotic assembly line could cost millions.
Adapting Existing Production Lines for Robotic Integration
Integrating robotics into existing Nike factories presents unique logistical hurdles. Retrofitting older factories for automation is significantly more complex and expensive than building new, automation-ready facilities.
- Retrofitting vs. new construction: Retrofitting existing production lines necessitates extensive modifications, causing production downtime and incurring substantial additional expenses. Building new factories specifically designed for robotic automation offers greater efficiency and long-term cost savings, but represents a larger upfront investment.
- Workflow redesign: Integrating robots requires a complete reevaluation of existing production workflows. Processes need to be redesigned to maximize efficiency and fully utilize the capabilities of the robotic systems. This often involves optimizing the layout of the factory floor and streamlining individual production steps.
- Specialized skilled labor requirements: Implementing and maintaining robotic systems requires a team of highly skilled engineers and technicians proficient in robot programming, maintenance, troubleshooting, and repair. Finding and retaining this specialized talent is crucial.
- Example: Adapting a legacy assembly line for a robotic stitching system may require reconfiguring the entire workstation layout, including conveyor belts, material handling systems, and safety features. This can lead to weeks or even months of production downtime.
Ensuring Quality Control and Maintaining Human Oversight
While robots offer incredible precision, maintaining quality control remains paramount. A robust quality assurance system is crucial to prevent defects and ensure consistent product quality.
- Error rates and quality assurance: Even the most advanced robots can make mistakes. Implementing multiple layers of quality control, including human inspectors and automated vision systems, helps identify and rectify errors promptly. Statistical Process Control (SPC) methods are invaluable for monitoring and improving production processes.
- Human-robot collaboration (HRC): Effective human-robot collaboration is key. HRC strategies involve designing systems where robots and humans work alongside each other, combining the precision of robots with the adaptability and problem-solving skills of human workers.
- Data analytics for continuous improvement: Monitoring robotic performance using data analytics helps identify potential problems and areas for improvement. This data-driven approach allows for the continuous optimization of robotic systems and production processes.
- Example: Employing human inspectors to visually check for defects after robotic assembly, or using vision systems equipped with AI to detect flaws in real-time, immediately halting the production line if a defect is detected.
Addressing Job Displacement Concerns and Retraining Initiatives
The introduction of robotic automation inevitably raises concerns about job displacement. Nike must proactively address these concerns through comprehensive retraining and upskilling initiatives.
- Reskilling and upskilling the workforce: Nike needs to offer comprehensive retraining programs to equip its existing workforce with the skills needed for new roles related to robotic maintenance, programming, data analysis, and advanced manufacturing processes. This demonstrates a commitment to its employees and helps mitigate potential job losses.
- Creating new job roles: Robotic automation creates opportunities for new specialized roles. These include robotic technicians, data analysts, AI specialists, and automation engineers. Nike can foster internal growth by providing training and career advancement opportunities in these emerging fields.
- Ethical considerations and social responsibility: Nike has an ethical responsibility to address job displacement concerns transparently and responsibly. This involves open communication with employees, providing adequate support during transitions, and ensuring fair compensation and benefits.
- Example: Training existing factory workers to become certified robotic technicians or data analysts, allowing them to maintain and program the robots, or analyze the vast amounts of data generated by the automated production lines.
Conclusion
Robotic automation in Nike sneaker factories presents significant challenges, including high initial investment costs, the need for extensive production line adaptation, ensuring quality control, and addressing job displacement concerns. However, by strategically addressing these issues through meticulous planning, significant investment in training and development, and a strong focus on human-robot collaboration, Nike can harness the transformative potential of robotic automation. Overcoming these challenges is key to the future of Nike's manufacturing processes, making robotic automation a vital investment for long-term success. Learn more about the innovative solutions driving this transformation in the sneaker industry and embrace the future of manufacturing with robotic automation.
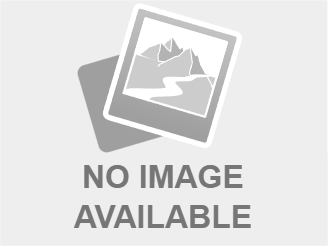
Featured Posts
-
Joint Effort South Sudan And Us Coordinate Deportee Return
Apr 22, 2025 -
Access To Birth Control The Otc Revolution After Roe V Wade
Apr 22, 2025 -
Pope Francis Death At 88 A World Mourns
Apr 22, 2025 -
Hegseths Military Plans Disclosed In Signal Chat
Apr 22, 2025 -
Analyzing The Difficulties Of Robotic Nike Sneaker Assembly
Apr 22, 2025