Why Making An All-American Product Is So Difficult
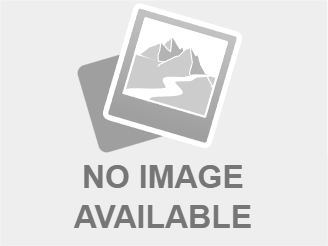
Table of Contents
The High Cost of Domestic Manufacturing
Producing an All-American product often comes with a significantly higher price tag compared to goods manufactured overseas. This increased cost stems from several factors:
Labor Costs
American workers command higher wages than their counterparts in many other countries. This difference significantly impacts production costs, particularly in labor-intensive industries.
- Textiles: The cost of producing clothing in the US is substantially higher due to labor costs.
- Electronics: Assembling electronic devices domestically is expensive, especially when compared to manufacturing in countries like China or Vietnam.
Statistics consistently reveal this disparity. For example, the average hourly manufacturing wage in the US is significantly higher than in countries like China or Mexico, making domestic production more expensive.
Raw Material Sourcing
Sourcing all raw materials domestically presents another significant hurdle. Many essential materials either aren't readily available in the US or are considerably more expensive.
- Rare earth minerals: These crucial components for many electronics and advanced technologies are largely sourced from China, making it difficult to create a completely American-made product relying on them.
- Certain textiles: Specific types of cotton or specialized fabrics might require imports, hindering the creation of a fully domestic product.
Even products seemingly made in America often rely on imported components, weakening their claim as a true All-American product.
Transportation and Logistics
Domestic transportation within the vast US adds considerably to the overall cost compared to globally sourced goods.
- Fuel costs: The price of fuel impacts the cost of transporting materials and finished products across the country.
- Distances: The sheer distances involved in moving goods across the US lead to increased transportation time and expenses.
- Logistical bottlenecks: Unexpected delays and congestion in transportation networks can further disrupt the supply chain and increase costs.
Navigating the Complexities of the Domestic Supply Chain
Building a robust domestic supply chain presents unique challenges for manufacturers aiming to create an All-American product.
Supplier Reliability and Availability
Finding reliable domestic suppliers who can consistently meet production demands is crucial. However, the pool of domestic suppliers is often smaller than the global network available to companies sourcing internationally.
- Specialized components: Sourcing unique or specialized components domestically may prove difficult, leading to potential delays or production disruptions.
- Capacity limitations: Domestic suppliers might lack the capacity to meet the demands of large-scale production runs.
Relying on a smaller pool of domestic suppliers also increases the risk of disruptions if a key supplier faces challenges.
Inventory Management
Managing inventory when solely relying on domestic sources presents additional complexities and costs.
- Just-in-time inventory: The just-in-time inventory model, common with global supply chains, might be less feasible with domestic sources due to longer transportation times.
- Holding larger inventories: To mitigate the risk of supply disruptions, manufacturers might need to hold larger inventories, increasing storage costs.
Potential delays or disruptions in domestic supply chains can severely impact production schedules and profitability.
The Skilled Labor Shortage in American Manufacturing
The shortage of skilled labor in American manufacturing poses another significant barrier.
Finding and Retaining Skilled Workers
Attracting and retaining skilled workers in manufacturing is a continuous challenge. Many young people are not choosing manufacturing careers, contributing to a skills gap.
- Training programs: Investment in comprehensive training and apprenticeship programs is crucial to develop a skilled workforce.
- Competition for talent: Manufacturing faces stiff competition from other sectors for skilled workers.
Addressing this skills gap requires a multifaceted approach encompassing education, training, and attractive career opportunities.
Automation and Technological Advancements
Automation is often presented as a solution to labor shortages. While true, the significant upfront investment required can be a barrier, especially for smaller businesses.
- Robotics and automation: Implementing robotic systems and automated processes can enhance efficiency and reduce reliance on manual labor.
- High initial investment costs: The high cost of automation can be prohibitive for some manufacturers, especially small and medium-sized enterprises (SMEs).
Regulatory Hurdles and Compliance Requirements
Stringent US regulations add another layer of complexity and cost to producing an All-American product.
Environmental Regulations
The US has stricter environmental regulations compared to many other countries. Compliance with these regulations adds significantly to manufacturing costs.
- Emissions standards: Meeting stringent emission standards requires investments in cleaner technologies.
- Waste disposal: Proper waste disposal and environmental remediation contribute to higher production costs.
Compliance costs can be substantial, making domestic production less competitive.
Safety and Labor Regulations
The US has stringent safety and labor regulations designed to protect workers. While vital, these regulations also contribute to production costs.
- OSHA regulations: Meeting Occupational Safety and Health Administration (OSHA) standards necessitates investments in safety equipment and training.
- Labor laws: Compliance with various labor laws adds to the administrative burden and overall costs.
Ensuring compliance with these regulations is non-negotiable but adds considerable overhead.
Conclusion
Creating a truly All-American product presents significant hurdles. High manufacturing costs, complex domestic supply chains, skilled labor shortages, and stringent regulatory requirements all contribute to the challenge. While the desire to support domestically made products is strong, understanding these complexities is crucial for fostering economic growth and creating viable solutions. Let's work together to find innovative approaches that make producing high-quality All-American products and domestically made goods more feasible, supporting American jobs and strengthening our economy.
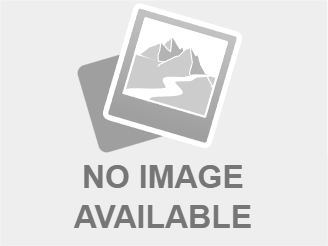
Featured Posts
-
Willie Nelson Celebrates His Roadies Legacy In Upcoming Documentary
Apr 29, 2025 -
Mets Fall To Twins 3 6 In Series Showdown
Apr 29, 2025 -
Los Angeles Palisades Fire A List Of Celebrities Who Lost Homes
Apr 29, 2025 -
Ryan Reynolds Celebrates Wrexham Afcs Promotion A Historic Moment
Apr 29, 2025 -
Ev Mandates Face Renewed Opposition From Car Dealers
Apr 29, 2025
Latest Posts
-
Trump To Pardon Pete Rose After His Death Examining The Announcement
Apr 29, 2025 -
Will Pete Rose Receive A Posthumous Pardon From Trump Analysis And Reactions
Apr 29, 2025 -
Pete Rose Pardon Trumps Post Presidency Plans
Apr 29, 2025 -
Johnny Damon And Donald Trump Agree Pete Rose Should Be In Baseball Hall Of Fame
Apr 29, 2025 -
Snow Fox February 11th Check For Delays And Closings Before You Travel
Apr 29, 2025