Why Domestic Manufacturing In The US Remains A Challenge
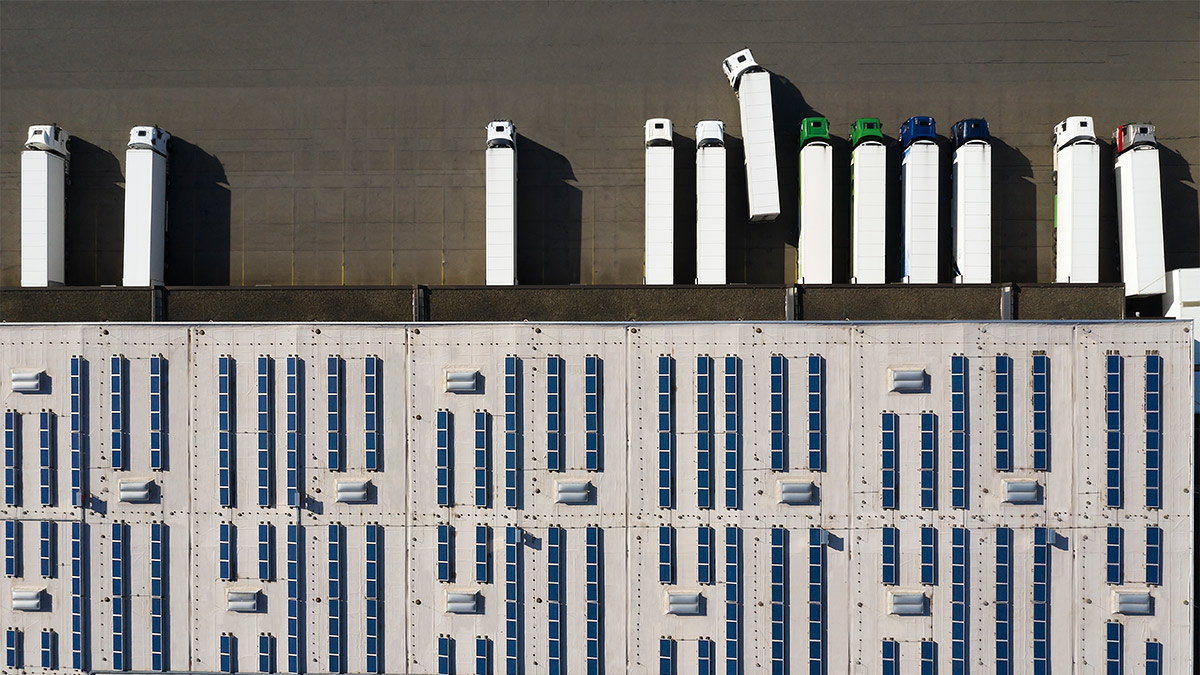
Table of Contents
High Labor Costs and Limited Skilled Workforce
One of the most significant barriers to increased domestic manufacturing is the cost and availability of labor. US labor costs are considerably higher than in many competing countries, significantly impacting the competitiveness of domestic production. This challenge manifests in two key areas: wage disparity and a skills gap.
Wage Disparity
The difference in labor costs between the US and other manufacturing powerhouses is stark.
- Minimum wage variations across states: Inconsistencies in minimum wage laws across different states create uneven playing fields and complicate national-level competitiveness.
- Unionization impacts: Unionized workplaces often command higher wages and benefits, which can increase production costs compared to non-unionized facilities in other countries.
- Benefits packages: Comprehensive benefits packages, including healthcare, retirement plans, and paid time off, are more common in the US than in many other manufacturing nations, adding to labor expenses.
- Healthcare costs: The high cost of healthcare in the US significantly increases the overall cost of employing workers compared to countries with universal or subsidized healthcare systems.
Skills Gap
Beyond the cost of labor, the US faces a critical skills gap in many crucial manufacturing sectors.
- Lack of vocational training: A decline in vocational training programs has resulted in a shortage of skilled workers trained in specialized manufacturing techniques.
- Aging workforce: The manufacturing workforce is aging, leading to a looming loss of experienced workers and institutional knowledge.
- Insufficient STEM education: A lack of emphasis on Science, Technology, Engineering, and Mathematics (STEM) education at all levels contributes to the shortage of skilled technicians and engineers needed for advanced manufacturing.
- Competition for talent from other industries: The highly skilled workers needed for advanced manufacturing are in high demand across various sectors, leading to increased competition for talent and higher wages.
Infrastructure Deficiencies
Outdated and inadequate infrastructure presents another major hurdle for US manufacturing. Aging infrastructure increases operational costs, limits efficiency, and reduces overall competitiveness.
Aging Infrastructure
The US infrastructure, including transportation networks and energy grids, is aging and in need of significant upgrades.
- Poor road conditions: Damaged roads and highways increase transportation costs and delivery times for raw materials and finished goods.
- Inadequate port capacity: Congestion at major ports leads to delays and increased shipping expenses.
- Unreliable energy supply: Power outages and unreliable energy supplies can disrupt manufacturing operations and lead to production losses.
- High transportation costs: The cost of transporting goods within the US is often higher than in countries with more efficient transportation systems.
Lack of Investment
Insufficient investment in modernizing infrastructure further exacerbates the problem.
- Funding limitations: Securing sufficient funding for infrastructure projects remains a persistent challenge.
- Bureaucratic delays: Lengthy permitting processes and bureaucratic hurdles delay infrastructure projects, hindering timely upgrades.
- Prioritization of other infrastructure projects: Competition for limited funding means that manufacturing-related infrastructure improvements are often deprioritized.
Intense Global Competition
US manufacturers face fierce global competition from countries offering lower labor costs, relaxed environmental regulations, and significant government subsidies.
Foreign Competition
The dominance of certain countries in specific manufacturing sectors poses a considerable challenge.
- China's manufacturing dominance: China's vast manufacturing capacity and low labor costs make it a dominant player in many global markets.
- Southeast Asian production hubs: Countries in Southeast Asia have become major manufacturing hubs, offering competitive labor costs and favorable business environments.
- Competition from developed economies with government support: Developed economies, such as those in Europe, often provide significant government support to their domestic manufacturing industries, enhancing their competitiveness.
Supply Chain Disruptions
Recent global events have highlighted the vulnerabilities of relying on foreign production.
- Geopolitical instability: Geopolitical tensions and conflicts can disrupt global supply chains, leading to shortages and delays.
- Pandemic-related disruptions: The COVID-19 pandemic exposed the fragility of global supply chains, causing widespread disruptions.
- Trade wars: Trade disputes and tariffs can significantly impact the cost and availability of imported goods.
- Reliance on single-source suppliers: Over-reliance on a single supplier in a foreign country increases vulnerability to disruptions.
Regulatory Burden and Environmental Concerns
Stringent US environmental regulations and safety standards, while essential, can increase manufacturing costs and present another significant hurdle for domestic manufacturers.
Stringent Regulations
Compliance with environmental regulations and safety standards adds to the overall cost of production.
- Compliance costs: Meeting environmental and safety regulations often requires significant investments in equipment and technology.
- Environmental impact assessments: Conducting environmental impact assessments can be time-consuming and costly.
- Stringent safety protocols: Implementing stringent safety protocols increases operational costs and complexity.
- Permitting processes: Navigating complex permitting processes can delay project timelines and increase costs.
Sustainability Demands
The growing demand for sustainable manufacturing practices adds another layer of complexity and cost.
- Green technologies adoption: Adopting green technologies and sustainable practices requires significant upfront investment.
- Carbon footprint reduction: Reducing a company's carbon footprint necessitates changes in production processes and energy sources.
- Waste management: Implementing robust waste management systems increases operational costs.
- Energy efficiency: Improving energy efficiency often involves investing in new equipment and technologies.
Conclusion
Revitalizing domestic manufacturing in the US presents a multifaceted challenge, encompassing high labor costs, infrastructure limitations, intense global competition, and a complex regulatory landscape. Overcoming these obstacles requires a comprehensive and collaborative approach. Addressing the challenges of domestic manufacturing demands a concerted effort from the government, private sector, and educational institutions. By investing in modern infrastructure, fostering a skilled and competitive workforce through improved STEM education and vocational training, implementing supportive policies that encourage reshoring and incentivize domestic production, and promoting sustainable manufacturing practices, we can pave the way for a more robust and competitive US manufacturing sector. Let's work together to overcome the obstacles hindering domestic manufacturing and build a stronger, more resilient American economy.
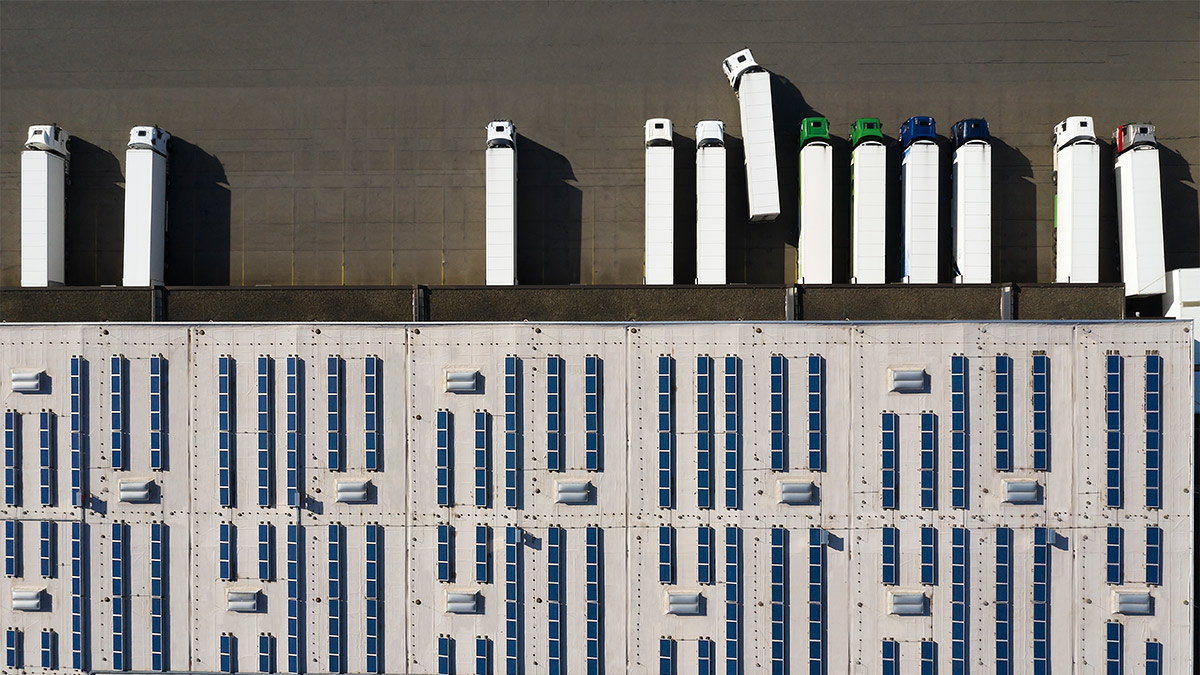
Featured Posts
-
Nyt Spelling Bee February 28 2025 Clues Answers And Spangram
Apr 29, 2025 -
Rent Increases Ease But Housing Costs Persist In Metro Vancouver
Apr 29, 2025 -
Dsp Mutual Fund Cautious Outlook On Indian Stocks Increases Cash Reserves
Apr 29, 2025 -
Reagan Airport Accident Shocking Details On Female Pilots Conduct Before Collision
Apr 29, 2025 -
Willie Nelson Announces New Album Oh What A Beautiful World
Apr 29, 2025
Latest Posts
-
Donald Trump Advocates For Pete Rose Pardon And Hall Of Fame Induction
Apr 29, 2025 -
The Pete Rose Pardon Years Of Lobbying Culminate In Trumps Decision
Apr 29, 2025 -
Pete Rose Ban Trump Promises Posthumous Pardon Criticizes Mlb
Apr 29, 2025 -
The Pete Rose Pardon President Trumps Statement And Its Implications
Apr 29, 2025 -
Will Trump Pardon Pete Rose The Push For Baseball Hall Of Fame Entry
Apr 29, 2025